The Polymerist is a free newsletter that publishes twice a week with one in-depth article on Tuesdays and a roundup and honest analysis of what happened in the world of chemicals on Fridays. Join the subscriber list to get free updates with honest analysis from someone with a PhD in chemistry from the industry.
In The News
Stanley Reed for the New York Times recently reported on the coming launch of General Electric’s new offshore wind turbine the Haliade-X which can be 12, 13, or 14 megawatts in power generation. When in operation a single Haliade-X 14 MW turbine can generate a maximum of 74 GWh of gross annual energy production (assuming constant output), which could save up to 52,000 metric tons of CO2 and is roughly the the equivalent of the emissions generated by 11,000 vehicles in one year.
To provide some perspective New York State consumes about 143.2 TWh of electricity per year. If New York State wanted to meet 100% of their electric needs with this new wind turbine (assuming these new wind turbines would operate at 100% of their capacity all the time) the state would need about 2000 Haliade-X 14 MW wind turbines installed. New York State consumes about 4% of all electricity in the United States.
To put these wind turbines in perspective to the rest of the industry and GE’s role Stanley Reed reports:
G.E. began making inroads in wind power in 2002 when it bought Enron’s land-based turbine business — a successful unit in a company brought down in a spectacular accounting scandal — at a bankruptcy auction. It was a marginal force in the offshore industry when its executives decided to try to crack it about four years ago. They saw a growing market with only a couple of serious Western competitors.
Still, G.E.’s bosses figured that to become a leader in the more challenging marine environment, they needed to be audacious. They proceeded to more than double the size of their existing offshore machine, which came to G.E. through its acquisition of the power business of France’s Alstom in 2015. The idea was to gain a lead on key competitors like Siemens Gamesa and Vestas Wind Systems, the Danish-based turbine maker.
A larger turbine produces more electricity and, thus, more revenue than a smaller machine. Size also helps reduce the costs of building and maintaining a wind farm because fewer turbines are required to produce a given amount of power.
GE currently has won the bid for installing turbines off the coast of Massachusetts for Vinyard Wind and 276 turbines off the coast for an offshore British project. I’ll quote Reed again here:
To make a blade of such extraordinary length that doesn’t buckle from its own weight, G.E. called on designers at LM Wind Power, a blade maker in Denmark that the company bought in 2016 for $1.7 billion. Among their innovations: a material combining carbon fiber and glass fiber that is lightweight yet strong and flexible.
A material combining carbon fiber and glass fiber that is lightweight yet strong and flexible is a bit of a simplification and is what I want to spend today’s newsletter talking about, which also ties in with my 2020 annual letter and my own Doctoral Thesis.
Composites
Let us start our talk on composites by looking at the Ashby plot above where the log scale Y axis is the Young’s Modulus or “stiffness” of the material and the log scale X axis is the density. At the bottom left we have flexible polymeric foams that might represent a mattress you would sleep on and at the top right we have ceramics and metals with diamond being the highest Young’s Modulus material.
Just to the left of the metals and ceramics domains, but above the polymers domain we have the composites domain. Composites are an excellent balance of high modulus with relatively low density when compared to the ceramics and metals and have a higher Young’s modulus than concrete (to be fair concrete is used for its compressive modulus). As you might guess the reason composites are between the ceramics and polymers is because they are essentially a mixture of fillers such as glass and/or carbon fiber in a polymeric matrix like epoxy or polyurethane resins.
Composites Are a Mixture of Two Immiscible Materials
Fillers - Glass Fiber, Carbon Fiber - Typically Inorganic
If you take a woven glass fiber or woven carbon fiber mat and play around with them they actually behave more like fabrics than you might expect. Woven glass fiber and woven carbon fiber are also typically sold like fabrics in rolls and pricing can be based on linear feet with a specific width and density (how tight is the weaving).
These woven fillers are pliable and in theory you could even make clothing out of them although a glass fiber t-shirt might be really uncomfortable. It then stands to reason that you could not make a wind turbine or car parts or rocket ships or space elevators with just the woven fibers. Infusing woven carbon fiber and/or woven glass fiber with thermosetting resins like an epoxy resin and allowing that thermoset to cure or fully polymerize is what gives the final composite it’s amazing strength to weight ratio in the Ashby plot above.
Polymeric Matrix - Almost Always Organic
Epoxy resins are what I studied in graduate school so I’ll talk about them here since they are what I know the best, but other thermosetting polymers can be used such as phenolic resins or polyurethanes. I will go in-depth into epoxy resins in another newsletter.
The reason why thermosets are so applicable composite manufacturing is because the polymerization happens around the fillers and the monomers or prepolymers are actually low enough in viscosity to infuse around the filler and as they polymerize they essentially adhere the fillers together and adhere to the fillers themselves.
There are many processes for making composites, too many for here actually, but to make things easier and to keep us aligned with wind turbines vacuum resin infusion molding is the best way to explain how to make a composite. The video below does a better job of showing how vacuum infusion works than I could ever write.
A few things to take away from the video would be that preparing the piece is time consuming. There is a lot of taping, bagging, and making sure the vacuum set-up is free of leaks. The second thing to notice is that the grade of epoxy resin is really important, the term low viscosity is used and this is primarily because you want the resin to flow relatively quickly through the carbon fiber before it starts to build molecular weight and eventually gelation.
The same principles apply at scale to wind turbine blades which are often actually two shells with some framing on the inside (also composites) that help provide strength. The longer the wind turbine blade is the more energy it can produce, but it can also be more difficult to produce. The blade shell below is from the Siemens SWT-6.0-154 and at the time in 2013 was considered the longest blade to go to production and had an output of 6 MW.
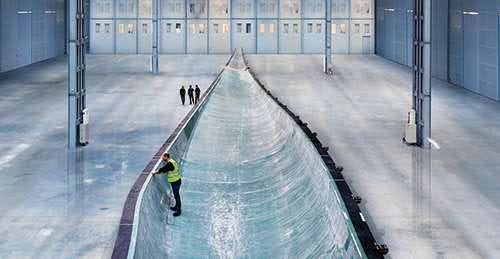
The new GE Haliade-X turbines will essentially have double the Siemens SWT-6.0-154 energy output and will have a 220 meter rotor diameter, about 42% larger than the Siemens rotor diameter. Production of Haliade-X blades will likely have to be localized near to where the installations are to happen because transportation of a blade of about a football field in length is challenging to say the least. Further, GE will need a lot of epoxy resin, glass fiber, and carbon fiber to make their new blades a reality so companies like Huntsman, Hexion, Corning, and Toray will likely be eagerly awaiting orders. It would be interesting if GE releases numbers on how many localized jobs a production facility for their wind turbines creates and how many people will be needed to support the infrastructure once installed.
Here is a great animation of a wind turbine getting made:
The Profound Conclusion
If you take anything away from this that is profound and thought provoking it should be that we still need to make chemicals to produce renewable energy generators like wind turbines. We need epoxy resins for composites, acrylics for paint, specialized polymers that go in batteries, and plastics for keeping our food fresh. The best way we know how to get all of these chemicals is from the extraction and refinement of oil and it will continue that way for some time, but I think eventually we might figure out the circular economy part and I think it will be in the next thirty years.
Tony
The views here are my own and do not represent those of my employer nor should they be considered investment advice.
This is also all provided to you free of charge so pay me back by subscribing and/or sharing with your friends and coworkers who are chemically inclined.