I saw this tweet this week and it made me think about what is overall going on in the chemical industry both in specialty and commodity chemicals/polymers.

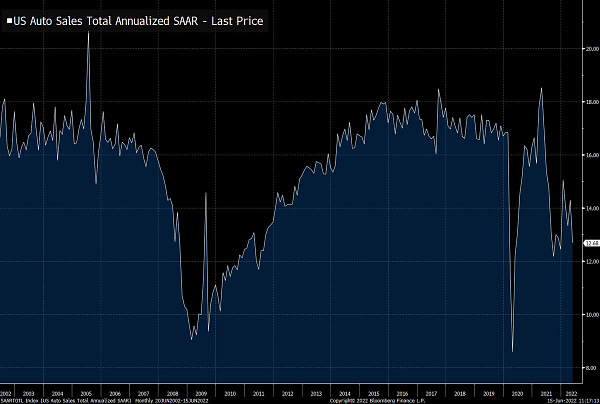
I think supply issues being a red herring is maybe partly true, but the reality is everyone is doing their best to maintain margins, secure their supply chain, and keep delivering product to customers.
Supply issues are real. Container prices are crazy high, if you can get one, and it’s difficult to find port and seafarer workers (appears worker shortages are a global thing not just North America). I’ve heard stories of shipping materials in containers where the cost of shipping the container is higher than the value of the material inside of the container. When this situation occurs I think it’s safe to say that the business buying the material will be looking for new suppliers and are willing to accept a higher raw material price as long as the total delivered price is lower. This desire to switch away from existing overseas suppliers or finding new suppliers is putting more demand on a smaller group of manufacturing locations, such as those located in North America, and this looks like an enormous amount of demand (even though it might be just slightly above what we had pre-pandemic).
From what I can see in the chemicals space the demand appears to be remaining strong based on 1Q2022 numbers. The high demand means that any sort of downtime or labor issues feels like a supply chain crisis to the customers. Demand is so high in some markets that existing capacity has a difficult time keeping up and delivering products. Add in a few operators getting sick or getting a better job down the street then a staff capacity issue also looks like a supply chain issue. Product not going out to meet orders just looks like a supply chain problem.
The logical thing now would be to build more capacity or have plans to build additional capacity. Ideally, this additional capacity would have been started a few years ago because permitting takes awhile. This capacity might look like an ethane cracker (ethane gets transformed into ethylene) being built in western Pennsylvania.
Reid Frazier for The Allegheny Front has some good recent reporting on Shell’s latest site and how it has created both hope for good jobs in the area as well as fears about legally permitted chemicals that can be released to the air. Shell’s cracker brings the promise of manufacturing jobs for locals who once had abundant jobs when steel production was big business in western Pennsylvania (it’s why The Steelers are called The Steelers). The question Beaver County residents needed to ask a few years ago: is making polyethylene in the county is worth it? Perhaps it’s too late for Beaver County, but I suspect other counties will be asking similar questions if new capacity is being planned.
Demand for chemicals and products downstream of chemicals such as coatings and computer chips brings us back to this concept of building additional manufacturing capacity in the United States. There was even talk about reshoring medicinal chemical manufacturing back in 2012. Meanwhile, over the last two years we have seen record demand for Covid-19 vaccines (also a completely new technology to manufacture) hit our manufacturing grid. I think it was amazing how quickly those vaccines were produced, but we are starting to see short supply of starting materials and raw materials such as plastic bags. There is only so much, “I need this now!” that our system can absorb without building a bunch of manufacturing locations.
Does the US or Western Europe really want these jobs back? It sounds like a good idea with record shipping costs, but what happens when those shipping costs decrease or “return to normal?” Will companies be willing to accept higher labor costs for the next 10, 15, 25 years so that they can have a robust supply chain?
If we re-shore or expand manufacturing capacity now this means we might solve the problems of today in a few years, but we run the risk of having too much capacity once shipping costs go back to normal. If shipping costs never go back to “normal” and higher prices are just here to stay then I guess we will be wishing we had built that manufacturing capacity years ago. The great thing about new manufacturing plants is that they in theory can be designed to be better than what we had 30 years ago.
I’m not sure new technologies such as biomanufacturing are quite ready to produce at scale and at cost either. Maybe in 10 years?
There is a great joke (I think its origins are Jewish). The pessimist says, “it can’t get worse than this,” and the optimist says, “Of course it can!”
One thing not mentioned is what materials are considered national security as well that we are willing to have domestically. Each country might ask themselves this question and have a different answer.
Is PE considered a critical material? If so how much volume and how far back into the monomer raw materials are as well? What about new material technologies? The questions can go on.
One way I believe this can be answered is truly defining the application usages in critical emergencies and work backwards. Should be at least a guide.