Hey There,
Every few months someone inevitably forwards me an article much like this one from The Atlantic. These articles usually share the following in common:
Chemical and plastic producers need to be held accountable for plastic pollution
We find plastic pollution in waterways and microplastics are appearing in alarming places such as human bodies
Recycling plastics doesn’t work and it’s a failed system
Banning single use plastics is the first step to combating this problem
The authors typically (not always) are running non-profits with missions to end plastic waste and pollution
There are allusions of plastic waste and global climate change being similar
Chemical or advanced recycling is a head fake and will be used to make fuels
What I find interesting is that banning single use plastics is a big strategy. If we banned every single use plastic utensil and food container we would still have plastic waste. Would we be banning garbage bags and condoms too or should those be reusable or maybe biodegradable? Should the bags that hold blood and plasma that are used in hospitals be reusable and/or biodegradable? If you go to a grocery store look around at what is packaged in plastic and then think about removing it and how long the food you buy might last without it. Banning single use plastics sounds good, it might even feel good, but it would ultimately change how we live our lives if we really went after everything that is truly single use. We also might have to cut down more plants to get their cellulose to make paper (maybe coat that in plastic to block water) to compensate.
The highest number reported around plastic recycling in the US was a recycling rate of 9% per reporting by the EPA. This number is also artificially inflated because the US sent a lot of spent plastic to developing countries where it wasn’t necessarily recycled. 9% rate of recycling is abysmal even if it were real. We have only gotten worse.
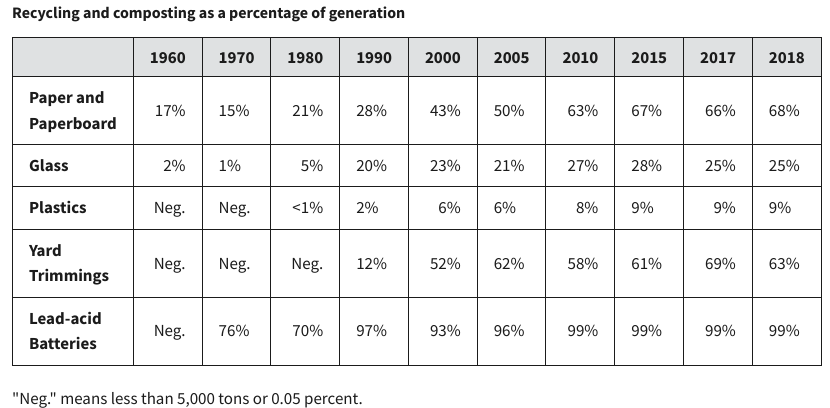
The questions we should be asking about plastic recycling is how do we get from 9% to 90%? Glass is only recycled at a rate of 25%, it’s about 2.7x more dense than plastic (if we assume all plastic is 1 g/cm^3), it requires more energy to melt, produce, and ship. I don’t see a bunch of articles calling for the banning of glass, but is 25% an acceptable recycling rate?
I’m not claiming to have all the answers around recycling. I did have a conversation with Rob Ianelli, he is the CEO of Ocean Works and Prjkt Polmr, which got me thinking about raw material qualifications. One thing that Rob wishes existed was a database of technical data sheets for “lots” of recycled plastic. If you have no idea what “lot” means it’s just a term that refers to a finite quantity of a raw material, typically produced on a singular day, by a singular factory or production line, until a finite raw material is consumed or the shift has ended. The idea is that limiting the finished good within some constraints will yield better control over end product quality and provide some level of traceability in the event of a recall.
Qualifying New Raw Materials
In the chemical industry we divide different batches or different days of production from a singular reactor or production line into “lots” to be better at qualifying that those materials were produced to a desired specification. For instance, if we are running a polypropylene compounding operation where we incorporate 10% by weight of glass fiber to be sold to a producer of train seats we might want to make sure that everything we produce contains about 9.8-10.2% glass fiber. Anything that falls outside of that range we might consider “off-spec” that either needs to get reworked or off-loaded to someone who will buy it. We might produce this product 3 days a week and thus might produce 3 different lots of material per week that get shipped to the manufacturer of train seats.
When manufacturing those train seats the manufacturer (our customer) is concerned primarily about lot to lot variability of raw materials from their supplier. If there is too much variability i.e. the glass fiber content is too low then this might lead to a failure mode of the seats breaking prematurely when in use, which might lead to keeping train cars out of service, and an unhappy customer. The seat manufacturer may even have some liability on the cost to repair the seats and/or the cost of the train car not being in operation. This may even cease production at the customer and the resin manufacturer might be to blame for the problems. Shit tends to roll downhill.
The train seat manufacturer likely has multiple raw material suppliers for the same raw materials. These suppliers are ideally in different locations and their suppliers are also different, which would mean that if a certain steam cracker and polypropylene producer were to go offline due to a once in a lifetime winter storm then the supply chain would not be seriously disrupted. If this seat manufacturer wants to bring in a new supplier they would typically put out a request for quotation (RFQ) and ask suppliers to give them a technical data sheet, samples of material, and potentially a certificate of analysis on the specific lot of material as well as a price.
Someone like me might be in the lab trying to qualify this raw material. When it comes to injection molding train seats a scientist or engineer might run a series of tests such as melt flow index, differential scanning calorimetry, and ash content (to see if there really is 10% glass). If things look good this scientist or engineer might run a manufacturing trial by ordering a few “lots of material” to ensure the manufacturing process, with the help of a process engineer, runs the same and that the seats passed their own quality checks. Usually these manufacturing trials will go until 5 different lots of material have been qualified and which point a commercial relationship might get formed and then that level of quality and consistency will become standardized.
The Problem No One Talks About
Now that you kind of understand raw material qualification and the need and desire for consistency we can talk about the problem recycled plastics have versus virgin plastic.
Recycled plastic provenance and composition is difficult to figure out. Material recovery facilities can often do a good job by sorting plastic types such as polypropylene and high density polyethylene, but are they all filled with the same filler, pigments, antioxidants, and UV stabilizers? This is part of what Rob was referring to when it comes to recycled plastics around technical data sheets.
As someone who might want to use this recycled plastic in a product I need to know that the raw material will be fit for purpose and I need to have reasonable knowledge that it will work before I test it. Once tested and in a manufacturing trial I also need to know that the quality will not change significantly, which means that I might need my procurement team to specify that it comes from a specific material recovery facility (MRF). The idea here being that this MRF processes the spent plastic of a community where consumption habits do not change significantly and thus the security on the quality of the recycled plastic.
A technical data sheet being available for recycled plastic is step 1 in getting it qualified by a buyer and that buyer needs to know that the quantity and quality will be consistent. By quantity I’d say a minimum significant quantity is a million pounds of plastic or resin per year. Depending on inflation recycled plastic could be anywhere from $1-3/lb in cost and it might track on the price of virgin plastic. Some recycled plastics cost more than virgin because the recycling process might be costly, but it could also be due to the demand.
Up until this point when I write “recycled plastic” I am referring to the mechanical process of sorting, washing, chipping, and extruding this plastic into pellets. This process can be costly and potentially not possible to run if the recycled plastic bales are of poor quality such as being mixed with a bunch of other plastic.
Imagine you bought a pound of coffee, but then realized 20% is actually saw dust, you would make shitty coffee. No one wants shitty coffee.
The Promise of Chemical Recycling
Chemical recycling of plastic is a viable method and it’s already being deployed at scale and showing profitability for rPET or recycled polyethylene terephthalate. I’ve written about this before and there is plenty of capacity being brought online by companies such as Eastman and Indorama, but the main message here is that the method could eliminate issues around recycled plastic quality. Glycolysis of PET to make rPET fiber is a big source of recycled polyester fiber in clothing.
Even if you are bringing in low quality PET bales from the United States which are contaminated with food particulates and other plastics the chemical recycling process could enable that plastic to be recycled. A mechanical recycler would have more difficulty in processes a “dirty” bale of PET, but in theory with enough glycol or methanol that dirty PET could be recycled and produce almost virgin quality PET out the other side.
My overall concern with chemical and advanced recycling is will the economics of the process work? PET is unique in that we can essentially cook it in ethylene glycol (anti-freeze), but a mixed plastic bale of high density polyethylene, polystyrene, and low density polyethylene might be a bit more tricky to turn into something consistent. These are the problems that pyrolysis recyclers are trying to figure out now. Cooking mixed plastics at high temperature to yield oil distillate products is tricky and there are other co-products that can be produced such as gases and carbon black.
Some of the issues here might be an immense amount of combinations of different plastics and how those chemical recycling operations might be able to handle or presort those materials before going through a specific process. Catalysts, residence time, temperature, and pressure will also influence any sort of pyrolysis operation.
Public Policy
We tend to think with our hearts. Banning single use plastics will reduce the total amount of single use plastics, but will it stop tooth brushes from ending up on our beaches? I don’t think so.
One great policy initiative I’ve seen lately has been a push for label free PET bottles. This has already been implemented in South Korea for all water bottles and by Coca-Cola, Evian , and Valser. The label on the bottle of Coca-Cola or Aquafina means that there is an adhesive keeping it on and it’s a piece of plastic that contains pigment and is often not 100% PET. A policy banning labels like this lead to better recycled plastic outcomes. The companies producing these bottles might need to innovate a bit to satisfy information requirements such as nutrition labels and branding.
Further, if we want recycling to truly work in the United States we need every home to have easy access to it. Below is a 2020 perspective on curbside recycling by an NGO that represents material producers around issues of recycling (i.e. take it with a grain of salt). There are real problems to be solved in recycling and many of them are related to infrastructure, participation by the public, and the packaging complexity that we just accept as consumers.
These problems of recycling shouldn’t be 100% on the consumers and it’s actually in the plastic and material producer’s best interest to invest money into the infrastructure around recycling. There is no technical silver bullet that will solve our material waste problems, but I think we spend too much time thinking about banning single use when the problems are much larger and complex than if I use a plastic spoon to eat my soup versus a metal. Even if we ban single use plastics here in the US there is still every other country that still uses them with even worse infrastructure for collecting, sorting, and recycling plastic.
A ban is a short term temporary solution to our problems at best. A chemical plant that produces polystyrene or polypropylene is going to find customers to buy their stuff. If it’s not single use plastic customers then it’s going to be somewhere else. That chemical plant operation will find customers even if the avenue of single use plastic is closed. We would still have plenty of plastic waste and we still wouldn’t have the infrastructure to handle it properly.
I actually prefer ceramic plates and bowls and with metal utensils or reusable wooden chopsticks when appropriate. Also, I love well made glassware. I’d be fine with banning single use plastic cups, utensils, plates, and bowls. Maybe it would make us slow down a bit and enjoy our meal times and coffee breaks as opposed to rushing off to work harder.
This is a nice summary, Tony.
I think there is a lot of promise in PET-to-monomers technology (i.e., regenerate TPA and EG) which can generally deal with contaminants pretty well (filtration) but is of course more energy-intensive than conventional processes. For other commodity polymers, there's not much you can do, and for stuff like PE, PP, or PS you either mechanically recycle it until it has no value, or pyrolyze it to oils / waxes, or burn it to generate energy.
There's lots of work going on in academia related to chemical recycling, but from what I can tell, it is focused in inventing new polymers that are more tractable. Some of the ideas are quite clever, but I don't actually think this approach is a good solution to the problem, at its current scale.
One of the really big and often overlooked issues (which you touch on) is the complexity of the waste stream. Caps, liners, multi-layer packaging, pigments, additives, etc. are a big barrier (no pun intended) to any type of recycling. This can create some interesting conundrums. Our family likes to buy frozen vegetables and fruit (think broccoli, mango pieces, etc.) and we find that we waste a lot less food that way. But the stand-up pouches they come in are multi-layer (I believe PET and PE) and not recyclable here.
Even simple things like printed labels or dyes can be a problem. The common green pigment used in plastics is Pigment Green 7, which is perchlorinated copper phthalocyanine. It's more than 50% chlorine by weight. What do you do with it?
At the end of the day the old saw "reduce, reuse., recycle" still has a lot of merit. I think effort expended on redesign for reduction and reuse of polymer materials would have a lot more value to society than effort expended on recycling. But that's my two cents....
Good stuff, and an interesting perspective. Based on what I've studied with chemcycling, I think we'll be seeing a lot of policies in the near future (especially within the EU) that will help the economics. Policies like requiring a minimum % of recycled plastic can help the economics of chemcycling drastically as the recycled plastic should command a hefty premium.
I think we'll also see PS chemcycling become more used. I believe Indaver P2C + INEOS Styrolution is starting to test PS chemcycling, and the literature seems to suggest that pyrolysis is quite effective in obtaining the styrene monomer (50%+ yield i think), with contamination/separation remaining a huge challenge. What's great about PS compared to PE/PP is that you don't have to go via the long-chain HC → steam cracking route, whose heavy footprint really makes PE/PP chemcycling hardly environmentally beneficial.
But yeah I think none of this will be possible without policies on companies to design inherently recyclable plastics -- none of the paper-plastic films or multi-compositional plastics. It's frustrating how much contamination from paper, organic materials, metals are in everything, and that's nothing the consumer can do really...