The importance of MetGen is difficult to understand without first understanding where we get the majority of chemicals and materials and where we might look to get them in the future. Our world is built on petroleum and if we want a future bioeconomy we need to think about using cellulose and lignin. If you don’t remember the details I’ll briefly refresh your memory.
Much of the world we experience utilizes chemicals that contain more than 6 carbons in the form of aromatic structures. Chemists might refer to these things as phenols, phenyls, or aromatics and from a chemical structure perspective they are how polymer chemists impart strength to synthetic polymers. These types of molecules are the building blocks for synthetic polymers such as polystyrene, phenolic resins, epoxy resins, amino resins, polycarbonates, and polyurethanes to name a few. These polymers go into things like insulation foam, wood coatings, structural adhesives, coatings for canned food, rubbers, anticorrosion coatings, engineered wood, composites, photoresist resins and more. These synthetic polymers keep our basic infrastructure up and running. Without them modern life would literally stop.
The only source of naturally occurring abundant aromatic structures occurs in lignin. A nice simple way to think about lignin is that it’s like the protective candy wrapper that keeps all of the microorganisms from eating the sugary cellulose in a tree or grass. Fungi can naturally degrade lignin through enzymes called laccases and peroxidases with the end goal of getting to that sweet polymerized glucose called cellulose. It takes fungi some time to get through the lignin and to the cellulose and this is why dead trees in the forest take a long time to get turned back into soil. Whereas I can open the wrapper on a Take 5 in about 2 seconds.
We separate cellulose from lignin all the time though in a process called pulping. It’s how we make paper. The cellulose pulp gets turned into paper while the lignin, in the form of “black liquor” is in a highly alkaline solution that eventually gets burned to power the pulp mill. A reader pointed out last week that acidification of black liquor tends to precipitate out a bunch of other chemicals such as tall oil and you can read more about it here.
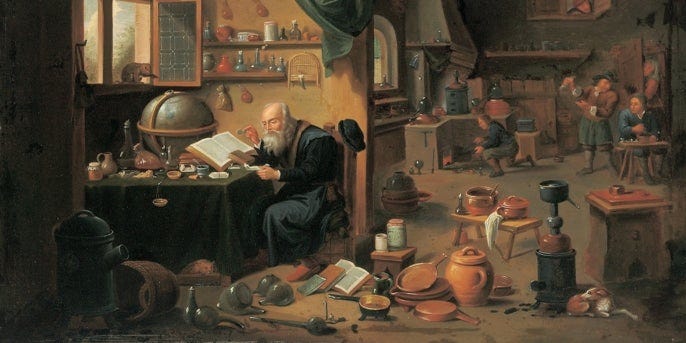
MetGen’s Technology
The crux and the engine behind MetGen that has me so hyped for their company is their fundamentals are based in enzymatic engineering. I’ve previously written about the importance of enzymes via Solugen and EnginZyme which you should check out if you haven’t already. If you haven’t then I’ll try and briefly summarize their importance.
Nature uses enzymes to do chemical conversions at ambient temperature both within and outside of cells. Enzymes are nature’s Philosopher’s Stone and can turn things that we find low cost and abundant, such as carbon dioxide and water, into food. MetGen’s enzyme can take what we have historically joked to be useless and only good for burning and make it a viable chemical feedstock.
Traditionally, enzyme engineering aims to either make a specific enzyme that does a specific chemical reaction either better at that reaction or more stable under more harsh conditions. An enzyme that doesn’t lose its specific activity at high temperatures could allow for better solubility of substrates and faster reactions and both lend themselves to more efficient production. It’s not just stability either. Sometimes, natural enzymes just don’t work in all the conditions we want and engineering them to do what we want is tricky and can take years. Just because an engineered enzyme is stable doesn’t mean it’s active and vice versa. We need both good activity and stability. Historically, stability has been found in enzyme immobilization.
MetGen has figured out to engineer some enzymes that can do the following:
Depolymerize lignin with minimal energy inputs at pH ~ 11 (this is alkaline)
Selectively change chemical functionalities within lignin fragments
Depolymerization and Refining
You can see some of the lignin depolymerization strategies in Figure 1 below (provided by MetGen). In my prior article about the bioeconomy I highlighted my own struggles as a polymer chemist trying to use lignin. The issue is that lignin’s size and complex structure was prohibitive enough that my team had to try and figure out some ways to depolymerize it by using strong acids/bases at high temperatures (greater than 100 C). This took significant energy and time and made the use of lignin more difficult due for the need for additional pre-treatment that wasn’t exactly free. Any cost savings we might have gained by using lignin would have been even lower. We were somewhere in the chemical oxidation and hydrolysis/solvolysis area in Figure 1.
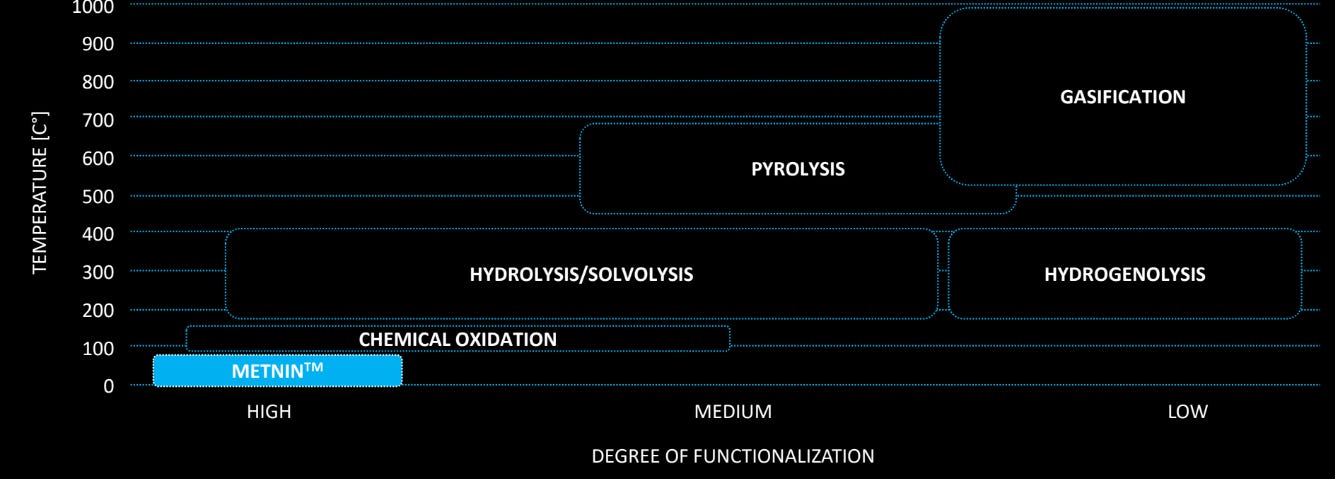
MetGen’s depolymerization and refining allows for three sizes of lignin polymers from the initial gigantic type that comes out of a pulp mill:
Large
Medium
Small
MetGen can do this depolymerization and refining in alkaline conditions, which is typically not possible for enzymatic treatment of lignin. Laccases are typically only active in acidic conditions such as pH ranges of 3-4, but the way you precipitate lignin from water is to add acid. Lack of lignin solubility under acidic conditions means it’s nearly impossible to get an enzyme that will degrade lignin with any speed because lignin isn’t soluble in an acidic solution. We might as well be stuck in a forest waiting for mushrooms to eat a tree. The hunt for an alkaline stable laccase has been a prize in the enzyme engineering community for decades.
In Figure 2 we can see MetGen’s depolymerization process. They mix their enzyme, with water, sodium hydroxide, air, and lignin together and out of the tank they get depolymerized lignin that can be fractionated into various different grades based on size.yields depolymerized lignin that can be separated via ultra filtration. The smaller the lignin the closer it resembles diphenolic or triphenolic structures and the larger fractions represent analogs that could maybe replace some current specialty polymers like an uncrosslinked phenolic resin or an aromatic polyester.

Increased Functionalization
In addition to depolymerization MetGen can also do some selective functional group manipulation. For the chemists out there that means being able to turn methoxy groups into phenols (demethylation) and alcohols into carboxylic acids (oxidation). For the non-chemists that means increasing reactivity with other chemicals to make new things that previously were not possible. All at room temperature. No heating required. Even easier than an Easy Bake Oven, but more downstream processing. Just don’t eat anything out of their process.
These additional chemical transformations open up MetGen’s downstream lignin products to even more customization and probable value in the marketplace. Specifically, demethylated lignin that is medium to small in size should be easier to replace phenol in phenolic resins. Small demethylated lignin fragments also have potential to be used as a multifunctional building block for polyether polyols in polyurethane foams. Lignin with a high degree of carboxylic acids can be esterified with alcohols and could also look like a classic tackifying resin (look out Kraton).
The New Crude Oil
If it’s not abundantly clear by now MetGen is developing the tools needed to make lignin a viable piece of biomass. Something similar occurred about 100 years ago when fractional distillation, steam cracking, and catalytic cracking opened up crude oil into being a viable feedstock platform. Being able to take biomass like lignin, especially as new types of lignin enter the market via companies like Origins Materials or others, and turn it into something useful feels a lot like figuring out ways to turn black sticky crude oil into the gasoline, polyethylene, and nylons that put the word “modern” in front of “world.” For MetGen, Lignin is the New Oil.
If we want to really move away from petroleum and all of its downstream petrochemical products with any sort of speed we need a new platform on which to build our economy. I previously declared that lignocellulose would be that platform, but to get there we need the tools to be able to make it viable in an environment where it competes with petroleum. MetGen is developing the tools we need to be able to utilize lignocellulose and make it a competitive alternative.
We can spend years arguing about the need to not use petroleum, but we need entrepreneurs figuring out the tools and products that provide viable alternatives. Proposing bans or shutting down petrochemical capacity with the hope that some alternative will materialize and take petroleum’s place is cruel and unusual. Let’s figure out the technology needed, make sure it’s a viable replacement through testing and commercialization, and then implement it at scale once profitable. Subsidies don’t hurt either. This is the way.
If you are interested in getting samples from MetGen to try out in your lab you should contact Dr. Petri Ihalainen at Petri.ihalainen@metgen.com or Dr. Liji Sobhana at Liji@metgen.com.
If you are interested in investing in MetGen you should contact Alex at Alex@metgen.com
Bioproducts people are fond of saying "you can make anything from lignin -- except money" .... so I liked your headline.
Nonetheless -- lignin (in its crude form -- black liquor) is important for providing energy for pulp mills. My understanding is that in modern operations, basically all of it gets burned, and this is an important part of the process economics in P&P (they don't need much "external energy"). So what happens to those operations when we start diverting lignin to other uses?
The future needs different lignins from various fractionation methods of lignocellulosic biomass.