Hey There,
Welcome back to the newsletter. To the ~45 new people here there is a loose structure I follow here and maybe check this out if you want to know why I’m writing. This is the portion of the newsletter focused on chemical product development and I typically pull from my own experience as an early career scientist. Things can get very technical, but I do try and zoom back out towards the end (no PhD required). If you ever want to chat reach out to me on Twitter @tpolymerist.
This issue of the newsletter is sponsored by:
Story From Graduate School
Tl:DR: I’m about to dive into a very technical story here around my own graduate work. I’m not sure how to tell it without it being technical, but I was in a time crunch to deliver biobased epoxy resins to a collaborator. I was trying to make something way more complex than I needed because I thought it was going to be better and I wasted months on this pathway. I realized there was an easier way and I took it. This became the foundation of my doctoral thesis. If this is enough for you then skip over to the don’t overthink it section.
For all you chemists in the audience:
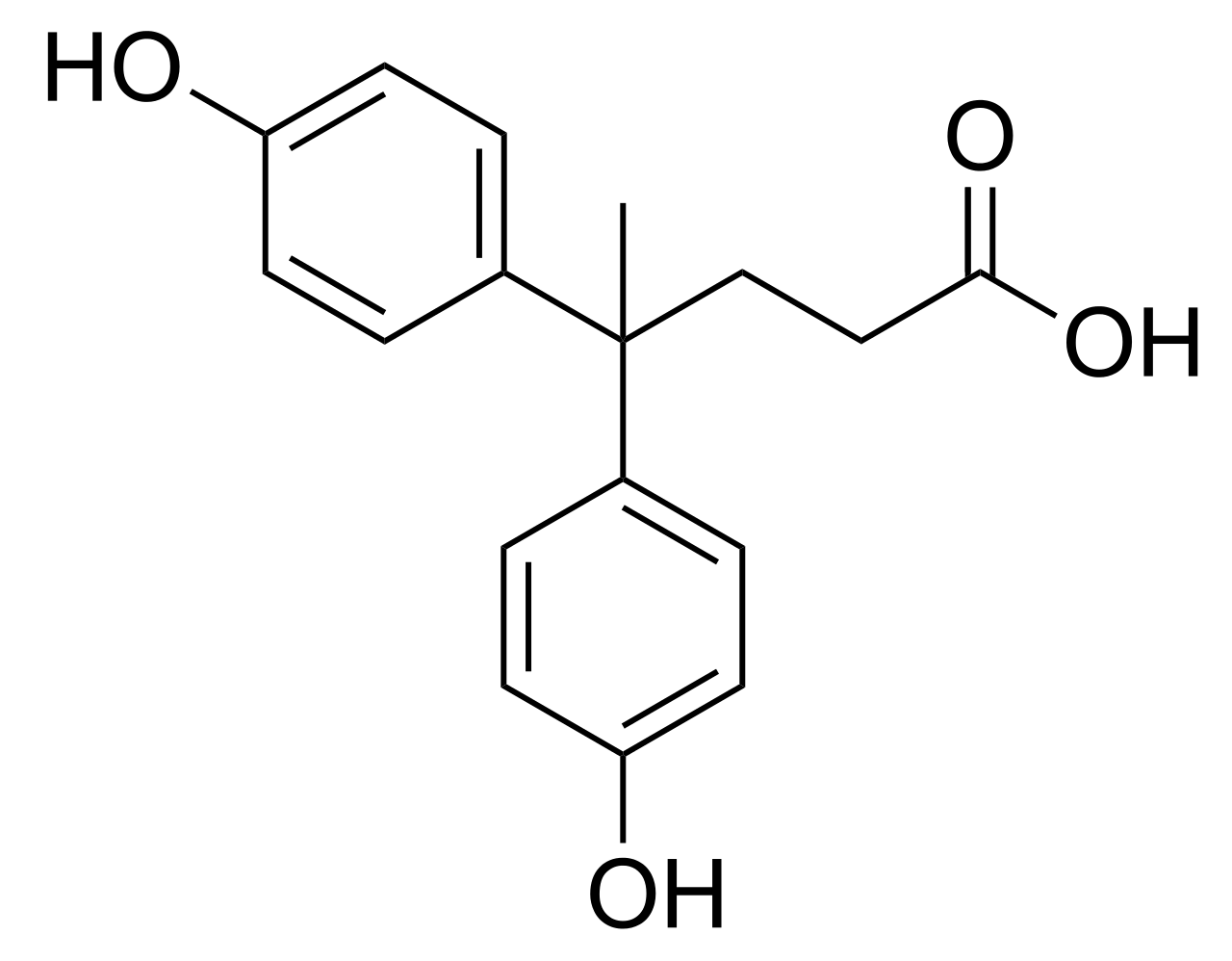
When I was in graduate school I was working on biobased epoxy resins based on a levulinic acid derivative called diphenolic acid. The problem that my collaborator and I were running into was what were we going to do with the organic acid? We knew that we couldn’t just glycidylate immediately due to the reactivity differences of phenols and organic acids (strength of nucleophiles) and when we tried it our NMRs looked more like a forest than a pure compound. We also knew we couldn’t run columns to purify anything because our collaborators (polymer engineers) wanted a minimum of 80 grams. Imagine running enough columns to get 80 grams of product. Then doing it over and over again as your collaboration progressed.
We also wanted something thermally stable and robust. What’s the point of working on epoxy resins if you can’t claim some crazy high thermal stability or glass transition temperature numbers? Stephen and I tried for a few weeks to make this amidation work, but we didn’t really get anywhere and our collaborators were asking, “when are we going to get our epoxy resins?” One route we tried was transamidation from the diphenolate ester, (e.g. the alcohol is a better leaving group), and I figured, “why don’t I just make these esters into epoxy resins?”
A few weeks later I had grams of epoxy resin, relatively pure yields via NMR, and best of all no columns. I was scaling up to liter sized flasks relatively quickly. We had a paper out to Biomacromolecules showing that thermal stability of a diphenolate ester was similar to its bisphenol-A counterpart and as the ester changes in structure so does the glass transition temperature and the viscosity of the resin. The whole concept of relating biobased epoxy resins to their structures became my doctoral thesis.
I learned two key lessons here:
Don’t overthink your problem before it appears
Once your problem appears it might not even be that bad
The desire to make an amide of the diphenolic acid molecule first was based on the hypothesis that it would lead to higher thermal stability, a more robust crosslinked network consisting of both covalent and strong hydrogen bonding (just like nylon 6,6). This was a great hypothesis, but we had other doctoral students waiting on us to deliver our part of the grant and we were in year 2 of a 4 year grant. Our problem had become making this amide epoxy resin when it should have initially been just making a new to the world biobased epoxy resin. Right after we published our first paper I remember my adviser got an email asking us why we didn’t pursue the amide version. Someone else came along just recently and figured out how to do what Stephen and I couldn’t do years later.
Don’t Overthink It
Stephen and I spent a few months trying to make something that we didn’t necessarily need at the time. We were trying to solve a problem that really only existed in our minds. We were predicting results we didn’t have and then trying to solve the problem that those results represented. At the time there was little to know information on diphenolic acid based epoxy resins. No one had made epoxy resins from diphenolic esters, amides, or anything else. We were overthinking it.
For me, going down the path of least resistance at the time was important because I was under a time crunch. I still published some great papers showing good fundamental science, and getting that first paper out led to a new collaboration and another cool paper. Plenty really. As graduate students I think we chase after what we think are big juicy papers that might get featured in Science or Nature. I remember having lunch with Stephen Cheng (former Dean at Akron’s School of Polymer Engineering and RPI alum) and I asked him if having just a few high impact papers was better than having a bunch of Biomacromolecules or Macromolecules papers. His response was something like this:
Are you crazy? Biomacromolecules and Macromolecules are the premier journals for chemists like us. You should be really proud to have one let alone many. Nature and Science papers often take years and huge teams of people working together. Publish good quality as often as you can. Don’t worry about impact factor.
One consistent thing I see is that smart people tend to overthink things. We see some chemical structures or a manufacturing process and we get asked to produce something new or cheaper or both and we come up with ideas. We then immediately see the problems of our ideas and we try and solve them without actually seeing if the problems we predicted come to fruition. If you do this you are then trying to solve for something that hasn’t even happened yet. If someone asks what you are doing you might sound like you came from the movie Minority Report—in a bad way.
Sure, if you know something will definitely be unsafe or cause something to be unsafe then don’t do it. My point here is that overthinking things can cause even more problems that we didn’t predict so instead of dealing with that original problem we predicted will happen we could also get trapped by new problems of our own creation that we never even anticipated in the first place. It’s quixotic.
A Word From My Sponsor
The team at Origin Materials is working to eliminate the need for fossil resources while capturing carbon in the process. Roughly half of global emissions are associated with the production of materials — a problem that no amount of solar panels or wind turbines can solve. By converting biomass into chemicals, Origin can tackle more than a few industries with a total addressable market of about 1 trillion dollars. Their first product is bio-based, carbon negative PET (polyethylene terephthalate).
Origin’s first plants are taking shape in Sarnia, Ontario, Canada and Geismar, Louisiana, USA. Once operational they’ll start fulfilling the $5.6 billion worth of signed offtake agreements and capacity reservations from companies like PepsiCo, Ford, Nestle Waters, Danone, Mitsubishi Gas Chemical, and Solvay. They are looking to hire passionate chemical industry professionals who believe in doing something different. If you’re interested in working for or with Origin, head to their website. The top 3 types of positions right now are:
Be An Experimentalist
If you are wise enough to not overthink your problems and the problem that you predicted does actually happen I view this as a good outcome. Your coworkers should be able to help you quantify the magnitude of the problem and might have advice on how to overcome it. Ideally, you’ve discussed your concerns with your coworkers and you’ve talked about at length before even doing any work. If it seems safe enough it might be worth doing just to experience it.
I’m not advocating that you try and see if something is nitroglycerin by hitting it with a hammer (true story from a professor of mine), but if you think some side reaction will occur and you view this as a problem just run the reaction and quantify it. You won’t know till you try and if you don’t try and you might just be stuck sitting at your desk thinking of reasons not to do something.
The problem might not even be that bad. Maybe everyone suffers from this particular problem you’ve encountered and everyone just deals with it. Is this a problem no one has encountered before and if you prove it’s existence would solving it lead to something patentable?
Further, once your problem is out in the open you can look at root cause issues. You can quantify this problem. If you are working on solving the problem that you are having you have something to communicate to your project manager about why things are taking longer than anticipated.
Problems are only scary if you are not in the problem solving business.
Very nice. I try to teach my students that coming up with novel, elegant approaches to technical challenges is often not a positive thing in industry (because the complexity that results is usually expensive) -- all the more so when one "falls in love" with those novel, elegant solutions.