The Second Half of the Big Six
Last week I wrote about polyethylene and polypropylene and how those two polymers make up half of the “Big Six” plastics. If you haven’t read that you can get to it here.
The next three plastics in the Big Six are polyethylene terephthalate (PET), polyvinyl chloride (PVC), and polystyrene (PS). There are three easy examples to illustrate the ubiquity of these plastics. If you have ever drank something out of a plastic bottle there is a 95% chance it was polyethylene terephthalate. If you have ever looked under a sink and saw some white piping that was polyvinyl chloride. If you have ever received something with some sort of molded foam packaging or drank something out of a red Solo cup then you have touched polystyrene.
The routes to these plastics are a bit more complex than polyethylene and polypropylene and there isn’t a nice little story about how invention of one led to another and then someone won a Nobel prize. The similarity that these plastics do have with one another is that they are dependent on the concept and production of platform chemicals.
Platform Chemicals
As the name might suggest these are chemicals from which other chemicals can be derived. One of the most important platform chemicals out there is benzene. When oil is distilled and fractionated there is a process called “catalytic reforming” where an oil fraction called “naptha” further processed with a catalyst to reform the chemical structure. Primarily, the goal is to get benzene, toluene, and xylenes otherwise known as BTX.
The toluene can be used as a solvent, but a major use is to transform it into benzene. Xylenes can also be used as a solvent, but para-xylene is often the most sought after. The other platform chemical relevant to this chapter would be ethylene. From ethylene, benzene, para-xylene, and chlorine we can make PET, PS, and PVC.
Polystyrene
React benzene with ethylene correctly and ethylbenzene is produced. Remove two hydrogens from the ethyl portion of that ethylbenzene and styrene is achieved. That is the way it has been done for just under 100 years, but in 2015 a new route to polystyrene was achieved in a single step. Vaughn and coworkers reported this significant discovery in Science—one of the most prestigious scientific journals on the planet. The differences in processes is shown in the figure below.
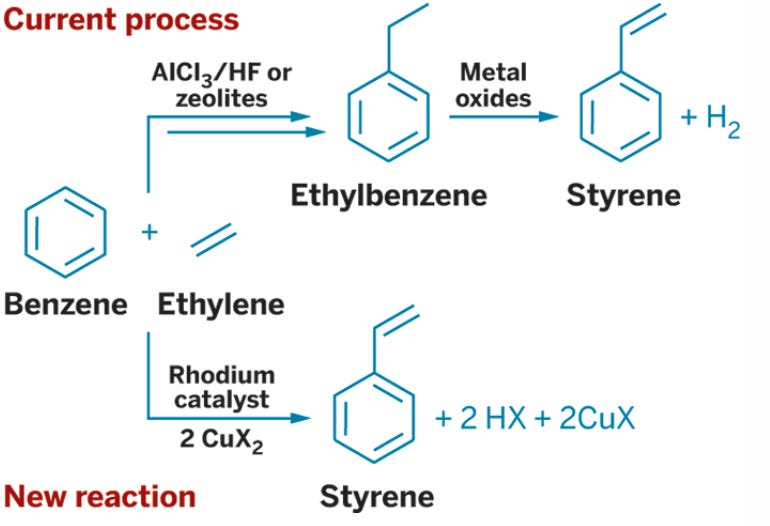
Rhodium is the most expensive metal on the planet and thus hinders the immediate commercial viability of the process. If the catalytic process can be done with a different metal then the synthesis of polystyrene becomes more efficient than the world’s best chemical engineers could achieve with the old process. If the new process were to become commercial it would then see decades of process efficiency gains as chemical engineers work to make it better.
Is making styrene and eventually polystyrene in this way better for our world? Well, it would make the process more efficient, lower prices, and if adopted by the current styrene producers it could provide significant shareholder value. This new process could also make it more difficult for any new plastic or polymer to compete and take its place.
Polystyrene is typically made via radical polymerization and is a common experiment performed by undergraduate chemistry majors. The polymerization methods for making polystyrene are not too dissimilar as polyethylene. Special catalysts (similar to Zieglar-Natta catalysts) can also produce different orientations of how the styrene monomers add together and can be used to help fine tune their properties for engineering applications.
The largest consumer of polystyrene is expanded or extruded polystyrene foam. Extruded polystyrene foam is made through an extrusion process and is more applicable to construction insulation products while expanded polystyrene foam is made from expanding small polystyrene beads in a mold. Expanded polystyrene foam is the form of polystyrene that most people are familiar with and it is also one of the most difficult polymers to recycle due to the low density as a result of the foam.
In terms of an insulating material extruded polystyrene foam has a difficult time breaking down, has a low cost, is light, is an excellent insulator and if building a home that should last for 30+ years is a good option for insulation. For sending me a computer monitor in the mail expanded polystyrene seems to only be used due to being able to absorb shock and because its low cost.
Unlike the other plastics in the Big Six expanded and extruded polystyrene are not typically accepted by recyclers. One issue with expanded polystyrene foam is that to transport it significant distance is uneconomical because it takes up significantly more volume than it weight compared to other plastics. Even if you were to get the foam all in one place it requires significantly more processing compared to the other plastics in order to be recycled.
Polyvinyl Chloride
The only plastic out of the big six that contains an atom other than carbon, oxygen, and hydrogen. Polyvinyl chloride or PVC is made from vinyl ethylene in a polymerization process similar to making polyethylene or polystyrene. The synthesis of vinyl chloride is non-trivial not because it is difficult, but because chlorine gas and hydrochloric acid are dangerous. The main routes to vinyl chloride is thermal cracking of ethylene dichloride with a byproduct of hydrochloric acid (HCl). The platform chemical of note here once again is ethylene and is needed by all of the plastics in this post.
The synthesis of ethylene dichloride follows either a direct chlorination of ethylene with chlorine gas to make ethylene dichloride or reacting ethylene with chlorine gas in hydrochloric acid. ICIS has a good summary of the process here. Either route you still need chlorine gas—one of the first chemical weapons used in World War I. Handling of chlorine gas is dangerous, but is often done with a high degree of safety in the chemical industry.
The main uses of PVC though are not necessarily consumer focused, but rather focused on construction products such as vinyl siding, windows, and plumbing pipes. PVC is not as good of an insulator for electrical wires as polyethylene, but it can be used for some lower voltage applications.
Of the big six plastics PVC is the least likely to end up in a recycling bin because it is not used in the everyday lives of most people (unless you are a plumber). PVC can be recycled, but the chlorine content means that it needs to be completely separate of the other plastics in the big six before it can be processed.
Polyethylene Terephthalate
The last plastic to be covered by me here and maybe one of the most ubiquitous that we encounter on a daily basis is polyethylene terephthalate (PET). The properties that really make PET stand apart from the other plastics are the gas barrier properties, clarity, durability, and versatility. We use PET for just about every bottled soda, water, juice, and tea. PET also makes great fibers and has been used in fishing nets and textiles for clothing.
The main route to PET is from oxidation of para-xylene to terephthalic acid and then esterification with methanol to produce dimethyl terephthalate, which is one of the two monomers needed for PET. The other monomer, ethylene glycol, is typically made from ethylene and oxygen to get ethylene oxide and then reacting that ethylene oxide with a hydroxide (sodium hydroxide, calcium hydroxide, etc) to make ethylene glycol.
Ethylene glycol and dimethyl terephthalate can then be reacted in the presence of a catalyst to yield polyethylene terephthalate and a methanol byproduct, which can be funneled back to the the dimethyl terephthalate process. PET is the only plastic in the big six to need two different monomers and it is the only plastic to also be made through a condensation polymerization as opposed to an addition polymerization.
Condensation polymerizations are reactions where during the polymerization another chemical is produced that must be removed from the reaction. Polyethylene, polypropylene, polyvinyl chloride, and polystyrene are all made through addition polymerization of one monomer where the monomer react with itself and no atoms are lost.
PET is built on the platform chemicals of para-xylene and ethylene. Already in covering the big six we can see that ethylene, propylene, benzene, and xylenes are completely necessary. The easiest route right now to get these platform chemicals is from distillation and fractionation of crude oil. There are other platform chemicals such as phenol, which is made from benzene and propylene, that get transformed into an even wider array of chemicals that we depend on everyday.
But wait, what about the sustainable chemicals that are made from biomass? I will cover this in another post, but the main problem that these chemicals face is one of scale. The incumbent technologies are established, efficient, and have low cost starting materials. New technologies are somewhat unproven, typically have higher cost platform chemicals, and might not be as efficient due to not having the same capacity of the incumbents they are trying to displace.
This is sometimes referred to as the Nylon Problem, but I will discuss this in a later post. Maybe next week.
Groupings
We can start grouping the plastics based on their structures. Polystyrene and polyethylene terephthalate both have aromatic rings as part of their structure due to being produced from both benzene and para-xylene. High density polyethylene, low density polyethylene, and polypropylene are all essentially aliphatic hydrocarbon chains. Polyvinyl chloride is by itself due to the chlorine atom.
If we were able to have all of these plastics completely segregated into pure recycled plastics this would be the first step towards developing a circular economy. This is primarily what the American Chemistry Council and Advanced Recycling Alliance for Plastics are trying to accomplish with their pilot of a secondary separation in the Northeast that I discussed last week.
You cannot solve a problem unless you understand it
Tony
The views here are my own and do not represent those of my employers nor should the views here be considered investment advice or medical advice.