Even if we could replace all of our energy generation with renewables such as solar and wind we would 1) still need to extract petroleum to make the materials we use everyday and 2) we would be sitting in the dark at night without a viable energy storage technology that we can scale. I’ve written extensively about what we need to do for 1, but I’ve given zero attention to how polymers will play a critical role in 2. Energy storage is just as important as renewable energy generation.
There are a whole bunch of interesting ways to store energy according to the EPA. We could pump water up a tower or to the top of the hill and let it fall to spin a turbine. We can compress air and let it release to spin a turbine. We can store energy in the form of heat and pump it around for when we need heat. Then there is everyone’s favorite–batteries.
Tesla and other companies have tried to do grid level storage with lithium ion batteries. The problem with traditional lithium ion batteries is fires. GM had to tell Bolt owners to not store their cars in garages for fear of fires until a recall could be performed. Tesla has had their share of cars still going up in flames. The FAA reportedly deals with at least one fire per week due to lithium ion batteries. This is just for electric vehicles and personal electronics. When batteries are big enough to keep whole cities or towns up and running at night we are talking about massive battery installations. Tesla had grid storage projects catch fire in 2021 and 2022. For those investing in these grid storage deals, safety and longevity of the investment are important factors to consider before investing millions even though it might be the right thing to do long term.
If you are familiar with fire testing then you know that Underwriters Laboratory (UL) is the leader when it comes to understanding why fires happen and how to design and implement fire mitigation systems. They also help write the standards and are the test lab when it comes to fire safety. From an S&P Global article on UL’s efforts to investigate fires by batteries:
UL's research into "the physics of failure" have revealed repeated problems with the flammable electrolyte in lithium-ion batteries that can cause "thermal runaway," according to Boyce, when an overheated cell turns into a self-perpetuating cascade. The problem can be triggered by internal defects or external stress factors, such as temperature, that cause one compromised cell to ignite adjacent ones, risking a large-scale fire.
When battery manufacturers are producing billions of lithium cells and a few failures happen within a battery pack from a single cell, it can result in a catastrophic event such as a battery fire. This is why lithium ion battery grid storage projects tend to be installed outside and why it might be difficult to get them into places like large residential or commercial buildings. LG Energy Solutions has had some challenges over the last couple of years with safety issues and product recalls in the automotive industry and their battery packs have also experienced battery fire issues in grid scale energy storage installations.
If you want an overview of why heat gets generated in a battery I suggest you check this paper out, but I think there is more complexity we need to reconcile due to the current lithium ion battery design.
Thermal Runaway
Our phones and laptops have batteries that utilize one of the lightest elements as their electrolyte–lithium. When charging a battery, lithium ions move through the separator to the anode (negative electrode) and when discharging the battery ions move from the anode back through the separator to the cathode (positive electrode) to complete one full cycle. I’m not here to tell you how batteries work, here’s a nice little blurb from the Department of Energy, but I do want to draw our attention to this concept of the separator and the role that it plays in lithium ion batteries.
The battery separator does a few important things:
It keeps the anode and cathode from touching
It allows free transport of lithium ions
In the event of a thermal runaway reaction it’s supposed to melt and stop the flow of ions
I once read that a major producer of lithium ion battery (LiB) separators had remarked that the market is relatively specialized in that you need specialty equipment to make the material, but it’s been commoditized. In just talking to various people involved in battery research when I mentioned separators they were a bit confused as to why anyone would want to switch away from the current technology because of the perceived associated costs. Aggressive expansion on the availability of materials, battery manufacturing capacity, and removing costs from the supply chain have resulted in significant cost reduction for lithium ion batteries over the last 10 years. All LiBs use ceramic coated polyolefin separators to keep their cathode and electrodes from touching and these polyolefins are made porous by stretching them till they almost break. When you stretch a semicrystalline polyolefin enough it elongates and then just before they break small tears and voids form in a process called crazing. Gore Tex is made from Teflon through a similar process.
The problem with a stress induced production process like crazing to form pores is that this deformation can lead to problems later during the deployment of these membranes as battery separators. There are a few things going on in a polymer that have stress induced voids or tears such as residual stress and wanting to go back to its original form. Polymers tend to remember their former shape and after being stretched they usually want to shrink given enough energy and time.
Here’s an experiment to try at home. Turn your oven on to 300-350 F and put some aluminum foil on a baking sheet and load in some plastic you’ve got hanging out around the house. Ideally put a soda bottle on there as well as the bottom of a takeout container (those black rectangular ones work well–keep the lid outside) and maybe tear off a piece of disposable grocery bag. I performed a variation of this experiment in my physical chemistry lab when I was an undergraduate. Put those materials in an oven for an hour or so and take them out. Notice anything different? The plastic will have shrunk. This is essentially how you make Shrinky Dinks. You can keep repeating this experiment over and over to see how long it takes your plastic to shrink at progressively lower temperatures.
Your plastic in the oven has shrunk quite a bit because it was produced by a molding process that caused stress to be induced in the plastic. If you repeat the oven experiment at progressively lower temperatures and maybe consider holding it for longer periods of time. If you heat up polyolefins too much you will get shrinkage and a film that was once 100 feet long might become 99 feet long. Shrinkage of 1% doesn’t seem like a big deal, but remember job #1 of the separator: keep the anode and cathode from touching. Shrinkage of even just a little bit can allow the anode and cathode to touch and that little bit of contact can set off a chain reaction that results in a catastrophic event–fire.
Commercial separators do attempt to mitigate this issue by using multiple layers of stacked polyolefin, such as the Celgard S1810 produced by Celgard, LLC, a wholly-owned subsidiary of Polypore International, LP, a Asahi Casei company. Celgard S1810 uses two exterior layers of polypropylene and a middle layer of polyethylene. The pores are still made by crazing, but the polypropylene has a higher heat deflection temperature compared to polyethylene so in the event the heat gets too high the polyethylene in the middle should soften and flow first and collapse the pores while the polypropylene still maintains structural integrity. Rheologically, it’s very difficult to get something like polyethylene to spread out and close all those pores, especially when it has been stretched. Instead of flowing and closing pores in the separator, polyethylene will want to shrink first and if the adhesion between the polyethylene and polypropylene layer is good it will try to pull the exterior polypropylene with it as it shrinks.
When the anode and cathode touch this is called a “short,” and it essentially means an immediate flow of electricity, the generation of heat, and this can trigger a thermal runaway event. The more heat we get in the cell of a battery the more likely it is for more of that heat to spread to other cells and cause other polyolefins to shrink. The more heat, the more shrinkage, and this problem can go from bad to worse to fire. A single cell failing through what is called “thermal runaway” means all of the neighboring cells are likely to follow. This might mean an electric car going up in flames or part of a grid storage project. Having a battery inside a building during a thermal runaway event could be disastrous if there isn’t a good heat management system in place.
The most cited or described initiation of thermal runaway that I’ve found so far has often been related to mechanical punctures or operating batteries for too long at high temperatures. This paper found that thermal runaway could be initiated through just a short burst of heat which can also cause the separator to fail and for shorts to occur. If you charge or discharge a battery too quickly, it can cause excessive heat. Operation of a battery in climates where there is excessive heat such as driving an EV in Texas or Southern California in the summer on a road trip could negatively impact your battery.
The thickness of the separator and the directness of the channels can impact how much battery you can fit into a physical space. If you want more information on battery membrane separators here is what I am told, “a canonical review,” but it’s about 10 years old at this point. Here is a review on thermal runaway and prevention using polymers. Here is another review on separators that is more recent. These references are just the start for someone outside of the industry looking to get up to speed on battery separator technology.
The current commercial separators for lithium ion batteries are not going through an innovation renaissance with respect to the large companies. The companies that make and supply these separators are interested in ensuring their manufacturing capacity is maxed out and that they are getting the best price possible. Their innovation will likely be marginal, such as making their separator better either in terms of small performance gains or reductions in cost.
There is a boatload of research in academia on separators, but for right now multilayered polypropylene and polyethylene separators that have holes generated from pulling on the separator membrane is the current commercial state of the art. As more electric vehicles get on the road in the next few years, the demand for lithium will increase. In order to squeeze more range, battery longevity, and better safety from the vehicles of the future, we need innovations in the materials that make up batteries. This includes the anode, cathode, electrolytes, and the separator. Right now, I think polyolefin membranes struggle to accomplish their role of keeping the electrodes of a battery from touching. We need something better.
Bodi Energy – Separator 1.0
Thermally stable and flame retardant polymers have been explored as battery separators to mitigate the safety hazards of commercial lithium ion batteries for use in EVs, consumer electronics and grid scale energy storage. Polyimide is the most thermally stable polymer known and has the potential to be designed into a badass battery separator.
I recently got to speak with Eric Donsky, founder and CEO of Bodi Energy, along with the inventor of Bodi Energy’s novel nanomanufacturing capabilities, Professor Yong Joo of Cornell University. Bodi’s mission is to develop safer and higher performing battery separator membranes for the batteries that go into a Tesla, Chevy Bolt, or a grid storage project. They are achieving this mission by electrospinning polyimide fibers into a thin porous membrane and then coating that membrane with a unique ceramic that further improves thermal stability, wettability of the electrolyte and a 4x improvement to ionic conductivity, which promotes much faster charge and discharge of the battery.
Electrospinning has been around for quite some time in academia. All you need to do is dissolve a polymer like a polyimide into a solvent such as dimethylformamide (DMF) and spin a droplet of polymer solution into a fiber using an electrical current. As the fiber forms and is spun from the nozzle containing the polymer solution the solvent evaporates and the fiber starts drying. Electrospinning can achieve super thin fibers and when layered into a mat or a web we can get a porous membrane. Tuning the process parameters such as current, polymer to solvent ratios, type of solvent, and how quickly the line is run can all impact the size and thickness of the membrane. Bodi’s electrospinning process has over a 10x faster production speed than conventional electrospinning and is capable of uniformly dispersing other raw materials into the fiber matrix, which is not currently possible with commercial systems.
Bodi Energy have also developed a room temperature curable ceramic that can be co-spun with their polymers, which allows a 2 in 1 process of both forming their membrane and coating it with their novel ceramic. Polyimide alone, just as a polyolefin alone, would not be great at conducting electrolyte solution through the membrane. The simplicity of Bodi’s ceramic process is that as the solvent is evaporated the ceramic migrates to the surface and starts curing at room temperature to form a unique core/shell structure. This sort of phase separation is common across many immiscible polymeric systems and the same phenomena happens with acrylics and waxes are used to form waterproofing coatings used to protect parking garages.
The membranes made by Bodi have been tested by numerous 3rd party labs and potential customers. In the technical presentation that Eric shared with me, three figures jumped out of the screen for me that demonstrated their membrane’s superiority.
The first was the shrinkage of the membranes as temperatures increase. You can see that Celgard (the raw polyolefin membrane) and the associated ceramic coated version shrink significantly even just above 100 C (212 F) while the Bodi membrane requires something above 350 C (662 F) to even start to show a small change. This is why Tesla has a cooling system to try and ensure their batteries never get too hot. A little too far above 100 C and shrinking becomes really obvious, even 1% shrinkage can have an impact.
The second figure shows discharge capacity at progressively higher energy densities against the cycle life of the battery cell. Figure 2 shows the Bodi separator compared to an all ceramic separator (too brittle to be rolled into a cylindrical cell) and a ceramic coated polyolefin separator. The goal of the test was to maintain the capacity as the battery aged in cycles (x-axis).

The third figure I think really highlights the safety the separator brings to testing thermal runaway on a battery cell. Figure 3 shows that as temperature is ramped over time in a battery containing both a commercial battery with a standard separator versus the Bodi separator the onset of thermal runaway is delayed by 60 degrees C and that the overall peak temperature achieved during runaway is 200 C lower. There also appears to be a significant amount of time where between 140 - 150 C there is a significant lag in the thermal runaway occuring.
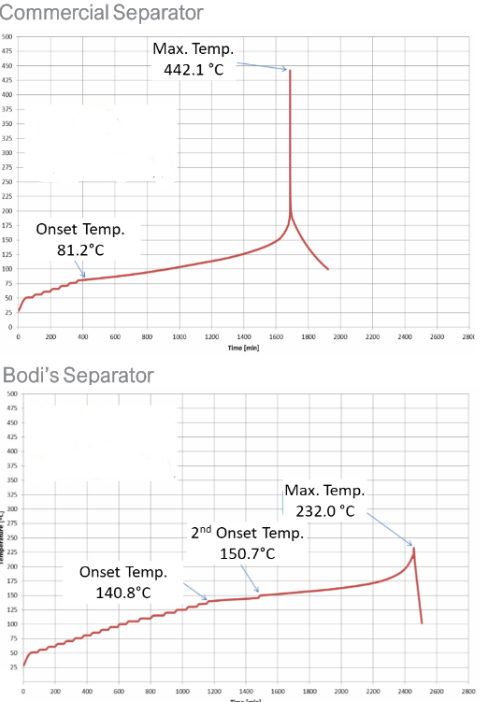
The other tests that I saw in the deck indicated that the first generation version of the Bodi separator enabled higher energy density at higher charge and discharge rates up to 3C. A “#C” charging/discharging rate indicates how fast a battery can be charged/discharged. A 1C charge rate is going from 0% to 100% in 1 hour (or 100% to 0%) and a 3C charge rate is 3x faster so 0-100% in 20 minutes. A Tesla supercharger for instance means charging at a higher C rate and doing too much of this can lead to overall capacity reduction of your EV battery. The first generation Bodi separator exhibited better capacity retention at higher charging cycles compared to a conventional polyolefin membrane. As far as I can tell the Bodi’s membrane is better than the conventional membrane in every way.
Now, the experienced polymer chemists out there might be thinking, Tony, the cost of a polyimide is significantly higher than that of a polyolefin. There is no way this could achieve cost parity. If we are talking about Kapton, where it’s a specialty diamine, and a requirement on molecular weight then you might be right. This is where Bodi version 2.0 comes in and why they are currently raising a Series A financing to complete development of their commercial separator and designing their commercial manufacturing line.
Bodi Energy – Separator 2.0
The vision that Eric and Yong laid out to me was one of bringing costs of their separator to the same as their polyolefin competition while maintaining their results from their prototype membrane. Their plan involves doing polymer synthesis during their process and using lower cost monomers.
The polyimides made by DuPont or other companies are very much fit for purpose for being used in electronics. The polyimides that are very much fit for purpose for being used as a battery separator might not be the same as those used for electronics. Bodi is using low cost monomers (they wouldn’t tell me which ones) to fabricate their own polyimides during electrospinning to get their costs down, maintain thermal stability, and able to be electrospun using greener and more sustainable solvents (e.g., cost effective, safer, etc.). No one should have to work with DMF in the future. There is a clear path towards Bodi pushing their membrane down the cost curve by being able to pair good synthetic polymer chemistry with good process engineering.
One thing you need to remember about the polyolefin membranes out there is that while the raw pelletized material might be cheap. Those pellets still need to be converted by melt blown extrusion of a 3 layer membrane followed by crazing and/or slitting down to specific membrane widths. They then still need to be coated in ceramic and the whole process sounds like a nightmare with regards to production of scrap material and quality control. When we think about the cost of the finished goods being sold to LG or Samsung to be wound into their lithium ion battery cells, we should be thinking holistically about not only the cost of the finished goods, but what value do they bring to the table?
I think part of the simplicity and the beauty of the Bodi process that I’ve read about and discussed with Eric and Yong is that raw materials go in on one side of their manufacturing line and finished goods come out the other side of the line. There is no production of a semi-finished good that needs to get shipped to another plant and converted by a different team. They aim to have complete control of their raw materials, their proprietary ceramic technology, and the manufacturing of their membranes. Raising their Series A would allow them to take their technology to the next level and start construction of a manufacturing line capable of delivering battery membranes to customers and enabling a safer future for both use of batteries and investment into their installation in the future.
I think the future of personal transportation is going to be electric vehicles (despite my desire for us to all live in a walkable utopia) and the future of energy generation will be solar and wind. We need safer and higher performing lithium ion batteries to make that future possible and we only get there through innovation in all areas of the battery including the separator that people consider to be a commoditized piece of plastic.
If you are thinking about investing, want to see more data, or want some samples of the material to try in your own batteries you should contact Eric Donsky at edonsky@bodienergy.com
Tony
This is not investment advice. You should do your own due diligence before investing into any company. I do not hold any financial interests in Bodi Energy or other battery manufacturing companies or EV manufacturers.
Interesting paper Tony. Thank you for sharing!
I wish all the best to Bodi on this tremendous endeavor. IMO, the electrospinning is a serious obstacle for commercialization. Nice technique but for academia purposes mostly.
Last year, I worked on this topic as well. I went even further, proposing a 100% biobased solution - a paper made from chemically modified cellulosic fibers. Improved wettability and conductivity, scavenger for HF formed by electrolyte decomposition, fire-resistant and thermal runaway mitigation through char formation. And very important from a commercial standpoint -the recipe can be manufactured on a paper machine.
Did I get the attention from battery world or even pulp and paper industry? Not at all. The separator is only a commodity product for them: a piece of plastic!