LG Chem Announces New Biodegradable Material
Will this material save us (the world) from our plastic waste problems?
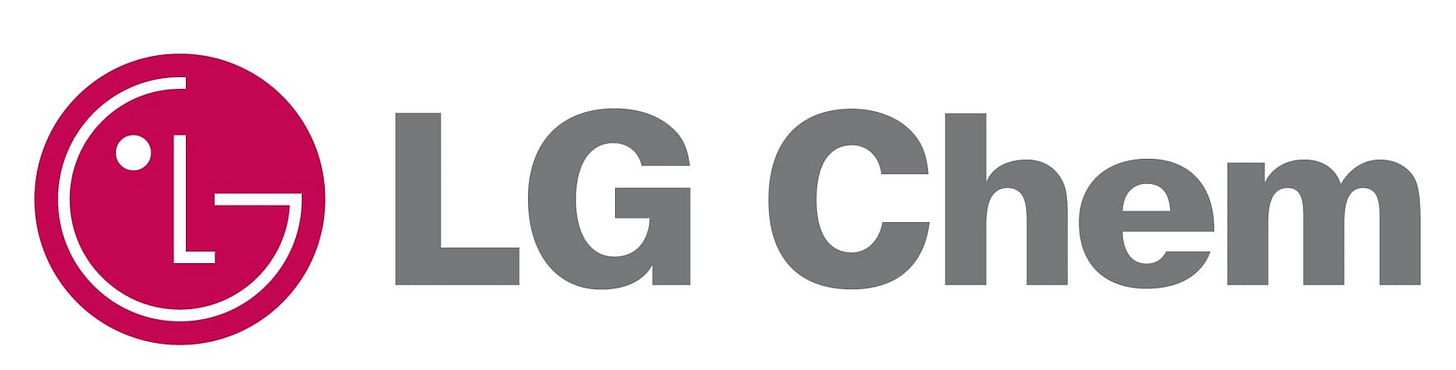
Welcome to The Polymerist a biweekly (twice a week) newsletter focused on the polymer and plastics portion of the chemical industry. If you are reading this for the first time please consider subscribing for a newsletter in your inbox every Tuesday and Friday morning. Tuesdays are deeper dives into specific topics while Fridays are highlights from the week.
If you are a subscriber and have enjoyed this newsletter please consider sharing it.
In the News
LG Chem is a Korean chemical company that produces a wide array of chemical products for end use markets such as personal care, energy storage, electronics, pharmaceuticals, and consumer packaging. LG Chem has recently announced they have developed a new material that is biodegradable and produced from renewable feedstocks with third party certification of the biodegradability. LG Chem hopes to enter mass production by 2025.
Material, Resin, Polymer—What’s the Difference?
One thing that I thought was interesting from this piece of news was that LG Chem specifically called their product a “material” and not a new polymer or resin. The word material implies that this could be a polymer blend of existing polymers/plastics that are already commercially available. Developing a new polymer is often not economically feasible due to all of the existing polymers that are produced at scale for much less money, existing regulatory approvals for production and use, and a wide array of upstream suppliers (aka the Nylon Problem).
I believe that LG Chem is likely launching some sort of polymer blend that may be composed of polylactide (PLA), polybutylene adipate terephthalate (PBAT), polybutylene succinate (PBS), or some other combination. I’ve written about PLA previously, but one problem with PLA is that it not flexible and it tends to break easily.
Think about opening an Amazon box and what is inside. Typically there is whatever was ordered plus some sort of packaging to keep the item from moving around too much, typically its some sort of flexible packaging containing a bunch of air.
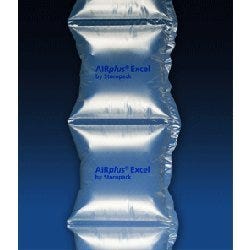
The actual plastic holding that air in place is probably some sort of polyethylene. LG Chem’s new material could act as a replacement here, which would mean that this packaging could eventually be compostable. The viability of compostable packaging material is only meaningful if there is a compost waste stream that can accept it, otherwise that high value compostable material goes straight to a landfill.
What is a Polymer Blend?
A polymer blend is much as the name implies, a blend of two or more polymers to yield a new material with specific properties. Typically in polymer blends there is a desire for the two or more materials to be compatible or able to mix together to form a homogenous material. For in incompatible material it’s helpful to think of oil and water not wanting to mix together and having to shake a vinaigrette dressing before using it.
Polymers can often act a lot like oil and water in that they do not want to mix. Melt blending a stiff brittle polymer like PLA with a softer and tougher polymer like PBAT should theoretically produce something in the middle and they do to some extent despite the polymers not mixing well together. The degree of how well two thermoplastic polymers can mix together also known as miscibility can be described by the Fox equation. Sometimes plastics just do not want to mix.
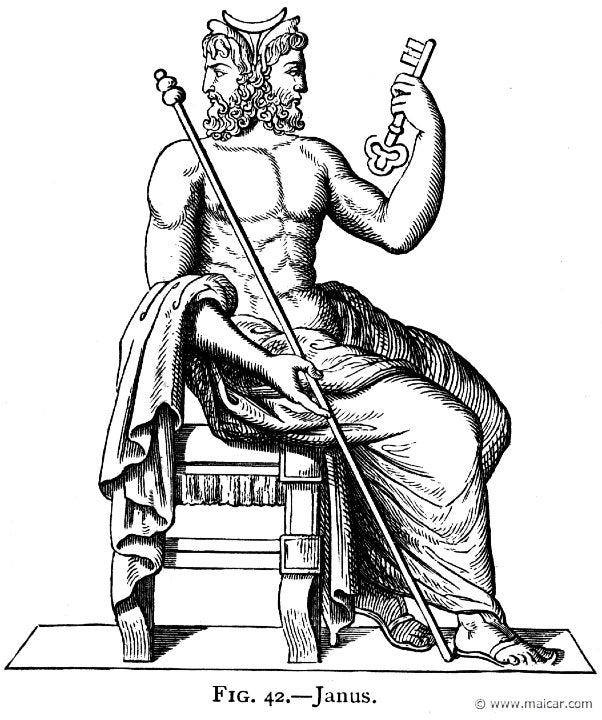
So if two polymers do not want to mix is that the end of the story?
Not quite. Chemists have known about the issues of polymer blending for decades and there are new technologies for getting plastics to mix. One method for improving the compatibility of two plastics like PLA and PBAT, two different polyesters, is to do something called reactive blending. The two polymers are mixed together in the melt, typically in an extruder with a catalyst, and then transesterification of the two polyesters occurs. The method of reactive extrusion essentially reacts one polymer onto the other and forces a reaction, which typically gives better results than just mixing the two plastics without a catalyst i.e. non-reactive extrusion.
The other method is to develop a compatibilizer or a “Janus Polymer.” The name Janus is derived from the Roman god of doors, gates, and transitions and he is often represented with a two faced statue. In polymer chemistry Janus is used to describe polymers or particles that have two different sides that have different preferred miscibility.
Block copolymers, specifically diblock copolymers are typically called Janus Polymers and can be used to help two immiscible or incompatible materials become miscible. The theory behind a “Janus Polymer or Particle” is that one part of the polymer mixes well with one material and the other side mixes well with the second material. The diblock polymer exists at the interface between the two materials and can help facilitate mixing. When melt blending PLA and using a compatibilizer with an immiscible material specific tailoring of properties can occur.
You can start a company based on diblock copolymers
The concepts of making diblock copolymers is gaining traction and a company called Interface Polymers was founded based on developing the technology. There are a whole host of areas in plastics where recycling is an issue due to incompatible materials. Recently, the recycling company around me has been rejecting people for putting food packaging bags into their bins. The issue around food packaging is that it is often a laminate of materials such as polyethylene, aluminum, and/or something called polyethylene vinyl alcohol or (EVOH). These other materials provide a barrier to gases such as oxygen, CO2, and other things that might cause food to spoil and are the reason why chips that are unopened can stay crispy for so long.
The problem with these laminated plastics is that they cannot be recycled with other plastic streams such as polyethylene, polypropylene, or polyethylene terephthalate. This is typically because the EVOH used in the food packaging doesn’t mix well with the other polymers and if they were melt processed together they could jeopardize tons of material due to poor mechanical properties. This is where a company like Interface Polymers comes in with their diblock polymer technology and enables the recycling of something like an empty pretzel bag that has previously been bound for a landfill. Interface Polymers is still a new company and it is unknown if they will be successful in commercializing their technology.
The Current State of the Art
Meanwhile, humans are finding ways to reutilize plastic fishing nets for consumer goods via Patagonia and Bureo, which is a straight forward concept of taking a pure plastic waste stream and converting it to something else. The video below details all of the benefits of doing this and I hope to see it used as a model for plastic recycling.
The Future of Plastics
I believe the future of plastics is going to be a mixture of biodegradable/bio-based plastic, recycled plastic, and making recyclable and biodegradable plastic from oil. I use the word plastic with an intent to describe the things we consider to be artificial such plastics like cups, straws, packaging, and fishing nets. Specialty polymers will likely stay the way they are, but the plastics we encounter on an everyday basis represent one of the biggest opportunities for change at scale. The only things standing in our way is creating a vibrant and celebrated secondary plastic market (Patagonia, Bureo, and others in the footwear/apparel industry are trying), an infrastructure and marketplace for composting at scale, and government policy to help start-ups in these spaces succeed.
The Polymerist
All of these views are my own and do not represent the views of my employer nor should they be considered investment advice.
Another great article...now if I can find a Janus for cellulose fibers in PLA or PE! Any suggestions?