The Polymerist is a free newsletter that publishes twice a week with one in-depth article on Tuesdays and a roundup and honest analysis of what happened in the world of chemicals on Fridays. Join the subscriber list to get free updates with honest analysis from someone with a PhD in chemistry from the industry.
In the News
Around the middle of December 2020 Borealis declared a force majeure on phenol and acetone due to a power outage at their Porvoo site. Borealis produces about 190,000 metric tons of phenol and 118,000 metric tons of acetone every year from the site. Force majeures are when companies stop production due to events outside of their control and will not be able to meet any sort of contractual sales obligation coming from the site due to the shutdown.
Hurricanes in the Gulf Coast of the United States that cause flooding can be a source of a force majeure, as can the low water levels on the Rhine river in Germany. Sometimes whole supply chains and the economics of a business are based on getting a barge of chemicals down a river from one chemical plant to the next and anything more expensive could invert the economics on a manufacturing operation that has low margins, but relies on large volumes.
But why should we care about phenol much less if there is a force majeure?
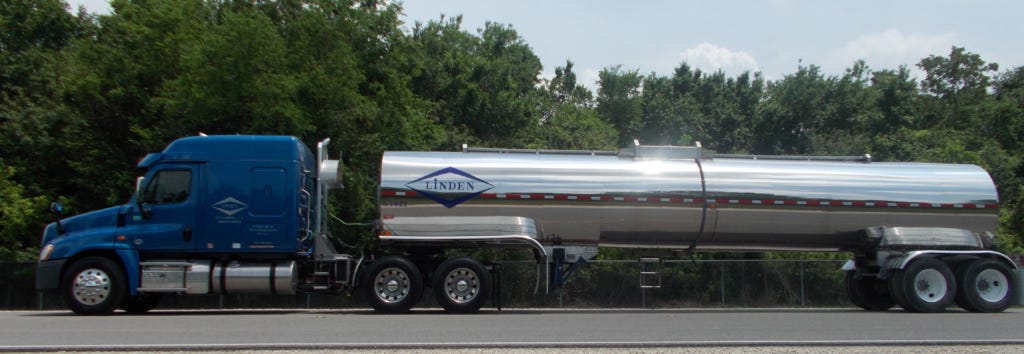
Platform Chemicals: Phenol
Phenol is the logo of The Polymerist and an important platform chemical for the production of many of our engineering polymers that enable our modern lives. Phenol and phenolic structures have played an important role in my own life from being the starting materials for epoxy resins that I would synthesize in graduate school to being monomers I would use to synthesize phenolic resins as a professional chemist. Phenol or phenol derived polymers fall under the category of “specialty polymers,” which means batch reactions and potentially very specific conditions to yield sometimes very specialized products designed for just one customer.
Specialty polymers are the “long tail” products before the concept of “long tail” was even coined, but in order for these types of products to be profitable the margins are either very healthy or the volumes are massive. I’ve heard of batch reactors reaching the 30,000 gallon volume, to give you a sense of what 30,000 gallons is a big bulk tank truck is about 11,000 gallons so you might need 3 trucks to pick up that 30,000 gallon batch provided you are hitting 80+% yield.
Below, I go into some details and provide additional resources for those that want to learn more.
Phenolic Resins
I only worked in phenolic resins for about 2.5 years, but there are chemists who spend their whole careers working in the field. If you want a really detailed resource on phenolic resin chemistry I point you to Phenolic Resins: A Century of Progress.
Leo Baekeland was the inventor of phenolic resins in 1907 (date of the patent being filed) and he is considered by many to be the “father of the plastics industry.” His discovery was that if you take phenol and formaldehyde in the presence of a catalyst such as an acid or a base you get something resembling a polymer and if the conditions are right you get a thermoset and water. This is a classic chemical reaction of A + B —> C + D where A is phenol, B is formaldehyde, C is your phenol-formaldehyde condensate, and D is water. Changing the ratio of the reactants A and B, also known as a mol ratio. If you are curious about what a mol is you might want to take a general chemistry class. Here is a Khan Academy playlist:
While phenolic resins are the first synthetic polymer they are also considered one of the best thermosetting polymers for their resistance to fire, high char yields, high glass transition temperature, and high modulus. You might use phenolic resins in aerospace composites or as a binder for the brake pads used in trucks and cars.
Think about doing 85 mph down the highway and slamming on your brakes to come to a stop. You stop by the brake pad creating friction against a piece of steel and the temperatures can get up around 500 F. If you want to cut steel you are going to need to use a grinding wheel, also known as a bonded abrasive, where the main workhorse of cutting is actually diamond. A phenolic resin helps hold a bonded abrasive together despite the high temperatures reached during cutting.
One of the largest volume uses of phenolic resin, at least in North America, is for making engineered wood. Oriented strand board (OSB) and plywood both account for a large volume usage of phenolic resin and the use of this polymer can result in some formaldehyde off-gassing after fabrication.
Formaldehyde off-gassing became a huge issue in the wake of Katrina with the FEMA trailers that used particle board before they were allowed time to shed the excess formaldehyde and as a result filled trailers with formaldehyde. The California Air Board then started instituting new regulations on formaldehyde emissions and the EPA began to studying formaldehyde even more due to its potential to be a carcinogen.
Due to this fear of cancer and regulation much of the engineered wood industry has been pivoting. There is a desire for non-formaldehyde alternatives and in the case of OSB there is a solution in form of pMDI or poly(methylene diisocyanate). That is a topic for another day and I’ve digressed quite a bit from my original topic here. Let us get back to phenolic resins.
Resoles
Phenolic resin synthesis can be represented by the A + B —> C + D equation, but it needs a catalyst and heat for the reaction to progress. A basic or alkaline catalyst (sodium hydroxide, etc) will form what is known as a resole and this typically happens when formaldehyde is in excess to phenol or a mol ratio greater than 1. The reason here is that phenol can react with formaldehyde three times and formaldehyde can react with phenol twice so excess formaldehyde ensures that a network of phenol-formaldehyde repeat units can form. Resole structures are complex and highly dependent on reaction time, temperature, catalyst type, catalyst loading, mol ratio, feed rates, and other potential co-reactants. Resoles typically have enough formaldehyde to yield a final thermoset polymer and it can be difficult to react all of the formaldehyde with all of the phenol. The excess formaldehyde and some formaldehyde generated while curing is primarily where the concerns from the EPA come from when it comes to engineered wood. Particle board and medium density fiberboard however utilize amino resins (story for another time). Making resoles is one part science and one part art because getting the final properties right is a bit like hitting a moving target.
Novolacs and Bisphenols
When phenolic resins are synthesized using an acid catalyst and a mol ratio of less than 1 where phenol is in excess to that of formaldehyde we can produce what is known as a novolac, which behaves more like a thermoplastic. Novolacs are in a sense formaldehyde poor and require additional formaldehyde to yield a thermoset, this is typically done in the form of hexamine, a formaldehyde ammonia adduct that looks like adamantane. When making novolacs the closer you approach a mol ratio of 1 the higher the molecular weight and the closer you get to gelation in the reactor (that is bad). The higher the molecular weight typically means higher viscosity, easier ability to grind the resin with hexamine in order to make a product that can be cured to yield a thermoset. Some of the larger volume uses of powdered novolac resins are for grinding wheels, brake pads, and acoustic automotive insulation.
Side Note: You do not just have to use phenol here. Cresols, naphthols, resorcinol, lignin, anything that looks like phenol and has sites that can participate in electrophilic aromatic substitution will work. Formaldehyde is also optional here, higher order aldehydes, terpenes, dicyclopentadiene, and mixtures of all the above. I hope the complexity of the chemistry starts to become somewhat apparent.
When mol ratios approach zero or when there is a huge excess of phenol we can get what is know as Bisphenol F (BPF) where the F stands for formaldehyde. Alternatively if we switch out the formaldehyde with acetone we get what is known as Bisphenol A or BPA, a starting material for epoxy resins and polycarbonates. Further, low molecular weight novolacs or novolacs that contain a mixture of BPF and higher oligomers can also be used to make multifunctional epoxy resins.
The excess phenol in these reactions are typically distilled off and then either reused in another product as a distillate or further purified to recover the phenol. Contrary to popular belief the chemical industry aims to minimize and reuse as much of the unused or unreacted molecules as possible for economic reasons. Generating a lot of waste or excess emissions means your manufacturing site needs to pay money and going over the permitted amount means you need to pay a lot more for every day you are in violation of the permit. If your “waste” can be the starting material for a new product then that “waste” now has value whereas before it was a liability.
Epoxy Resins
If you want an amazing resource on epoxy resins I suggest you read Epoxy Resins by Ha Pham and Maurice Marks in Ullman’s Encyclopedia of Industrial Chemistry. This reference was invaluable to me for my PhD and it holds an immense amount of basic information that to me is unparalleled.
The first liquid epoxy resin was synthesized by Sylvan Greenlee in Louisville Kentucky which he submitted to the United States Patent Office in 1948 according to Hexion. The earliest patent I could find actually has a filing date in 1949. Greenlee’s synthesis essentially involved adding bisphenol A (BPA) to an aqueous solution of caustic and then adding epichlorohydrin and more caustic soda and removing water until a taffy like substance had formed. Greenlee’s work would be expanded on by others at Shell and Dow and the modern epoxy resin business was born.
In the 1950s polymer science was very new, remember that Hermann Staudinger doesn’t win the Nobel Prize for polymers until 1953. Up until then in terms of thermoset polymers the best technology at the time was phenolic resins, which were prized for their chemical resistance, ability to be molded, and temperature resistance. One of the drawbacks about phenolic resins is that once they were fully cured they became very brittle and they were difficult to mold due to the curing reaction being a condensation reaction that I covered earlier and small molecules like water, formaldehyde, and/or ammonia would be released. These molecules could be trapped in the bulk of the polymer or create voids and defects in the final material.
When epoxy resins came out and they had the ability to become thermosets with the addition of polyamines or diamines and it was in a sense revolutionary because there was no condensation reaction. There were no small molecules that had to escape during curing and this is known as an addition polymerization where A + B —> C. A is the epoxy resin, B is the diamine or polyamine, and C is the cured epoxy resin. The great thing about addition polymerizations is that all of the atoms are kept within the system so nothing is lost. Chemists had also figured out how to make liquid epoxy resin systems and liquid polyamines or diamines so that when mixed together an epoxy resin system was still a liquid that could flow while it was also polymerizing. The time from mixing to until it was unworkable for a particular process is known as a pot-life. A 5 minute epoxy resin from the hardware store to fix that broken coffee mug handle has, as you might have guessed, a five minute pot life. Mixing together an epoxy resin system is a polymerization that most people do not realize they have done. There could be some great at-home lab experiments done with epoxy resin from the hardware store.
This combination of being a liquid that could be painted, rolled on, moved around by vacuum and also not emitted any other molecules during the polymerization led to the development of epoxy resin based composites, coatings, and adhesives. I wrote about wind turbines last week and despite composites being about 60-80% glass or carbon fiber filler the other 20-40% of epoxy resins matrix is just as important because the low viscosity of composite grade epoxy resins allows for filling of all the potential voids in a composite while also providing an amazing balance of heat resistance, strength, and toughness.
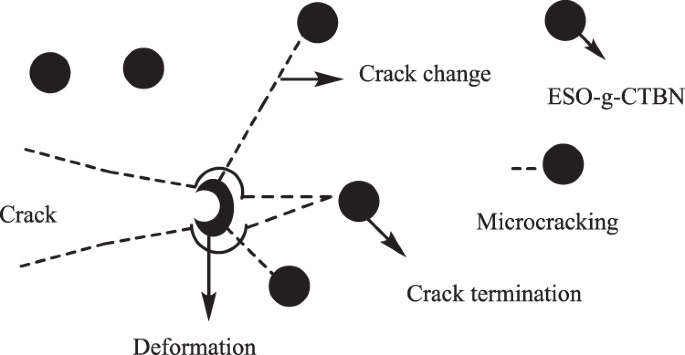
Toughness
The concept of toughness is related to fracture mechanics or how something might fail catastrophically. Typically what happens in fracture as pictured above a crack might form due to a void or small defect on the surface of the material, which could be from normal wear and tear or something hit it really hard. When stress is applied to the material a crack could form from the defect and the ability of the polymer to stop the crack from propagating throughout the bulk of the material is known as fracture toughness. Now when comparing an cured epoxy resin to that of a cured phenolic resin the cured epoxy resin is typically tougher than the phenolic resin, but material scientists also have useful ways to stop crack propagation in bulk materials such as adding bits of rubber as shown in the picture above.
These little bits of rubber are softer and squishier than the matrix that they inhabit and because of the liquid ability of epoxy resins things like rubber can be easily dispersed into the resin and stay dispersed during cure. The softer rubber helps absorb the crack propagation energy and help terminate cracks before they become catastrophic, which can extend the service life of many epoxy resin based materials. Further, because the rubber doesn’t actually mix into the epoxy resin system the thermal stability is still maintained.
Electronics
Epoxy resins are ubiquitous for composites used for wind turbines and boats, anti-corrosion coatings to protect bridges and metal structures, and as high performance adhesives in holding cars together in place of rivets. One use not often talked about is that epoxy resins are in electronics. The inherent high thermal stability and toughness of cured epoxy resin make them ideal for electronics that can get very hot and can even enable conductivity if formulated with silver nanoparticles or other conductive fillers.
Phenolic resins also play a role in electronics fabrication with photoresist resins as shown in the picture above. Novolacs are the preferred phenolic resin here and purity of the material is critical. Glass transition temperature and monomer selection all play a role in how the photoresist behaves during use. This is a useful resource if you want to learn more about photoresists.
In Conclusion
If you are a fan of wind turbines, computers, light weighting automobiles for better gas mileage and improving the range of an electronic vehicle, or making sure that our metal infrastructure doesn’t collapse due to corrosion then you are dependent on epoxy resins. If you enjoy being able to stop your Tesla, airplanes, or self driving trucks then you will need a phenolic resin. What I’ve written here is topical. There is so much more complexity and broader end markets than I have time to write about here.
In order to make epoxy resins and phenolic resins you need phenol and ultimately you need oil, at least for the next century. So even if we manage to get to some sort of utopian world of self driving electric cars, 100% renewable energy, and remote working through computers and the internet we will still need some refined oil to make the polymers that enable our modern lives. Maybe someone will figure out how to make phenol from mixed plastic pyrolysis?
Weather and climate change are only going to exacerbate supply chain complexity and ultimately the economics of the chemical industry and couple this the oil industry going through big changes and we have a recipe for uncertainty in the chemical industry for the next few years. Research into alternatives to oil in the last ten years for chemicals may be more useful than we think in the future.
Tony
If you have any tips email me at polymerist@substack.com
The views here are my own and do not represent those of my employer nor should they be considered investment advice.
This is also all provided to you free of charge so pay me back by subscribing and/or sharing with your friends and coworkers who are chemically inclined.
This was good stuff. Keep it up!