Solving the Plastic Waste Problem: Part 3
Chemical recycling could help raise the price of single stream and mixed use plastic waste.
If this is your first time seeing this series I have written previous posts that are worth reading that will help put this into context with Part 1, Part 2, and the Black Friday edition (Part 2.5). The post on Trash to Money will also be a helpful primer.
If you haven’t subscribed to the newsletter please consider doing so because it is free and lets me know you care.
If you are a subscriber please consider sharing and is also another way to show me that you appreciate what I am attempting to do for free.
Closing The Loop
In parts 1 and 2 of this series I talked about how we make the majority of plastics that are commonly referred to as the Big Six. These plastics are made from chemicals that come out of an oil refinery and the chemicals are often referred to as platform chemicals because they are the platform that supports the plastics and specialty polymers industry. You can make all of the big six polymers and much more from ethylene, propylene, benzene, para-xylene, and some things like oxygen and chlorine gas.
A barrel of crude oil is relatively useless until it is distilled, fractionated, cracked and/or reformed into useful platform chemicals or fuel. A ton of mix-plastic recycling is can gain enormous value when separated into the specific polymer streams on their recycling symbols of 1-6 and/or turned back into the platform chemicals from which they were derived and then repolymerized as needed. This means there are two routes to reusing mixed plastic raw material streams and we should look at mixed plastics similar to how we might look at a barrel of crude oil: A useful carbon source once it has undergone the necessary separations and processing to yield something of sufficient purity to where a well defined chemical reaction and processing can be performed.
Part 3 will focus on plastic pyrolysis or as it is also known chemical recycling.
Recycling Route 1: Mixed Plastic Pyrolysis
What is Pyrolysis?
Pyrolysis is the act of heating up something without the presence of oxygen, typically in an inert atmosphere like pure nitrogen or argon. The concept of pyrolysis has been around for quite a long time and it is how coal is transformed to coke, how polyacrylonitrile is converted to carbon fiber, and how we can make hydrogen out of methane.
Pyrolysis of most carbons produces gas, liquid, and solid products. The temperature, duration of the process, and use of a catalyst can all play a role in the composition of the yields of liquids, gases and char produced during pyrolysis. The catalyst plays an important role in determining what types of pyrolysis products come out of the pyrolysizer as well such as the composition of gases or liquids. A simplified schematic of what a pyrolysis set-up might look like can be seen below in Figure 1. Volatile liquids get captured in the cold traps, the inert gas escapes, and the mixed gas products continue on further while the char stays behind in the main heating vessel. Essentially, plastic goes in and then liquid, gases, and char come out the other end.
The thing to take away from pyrolysis of plastic waste is that under the right conditions, chemicals that resemble oil distillates can be produced. If pyrolysis is done near or next to a cracker or catalytic reformer those pyrolysis products could be transformed or purified using existing technology developed for oil based products into the feedstocks that produced the plastics in the first place or something else that the market might need.
The advantage of pyrolysis is the flexibility to produce fuels, lubricants, plastics, or more specialty chemicals. The flexibility of pyrolysis is why I think it will be a preferred method of recycling, especially when it comes to somewhat impure, but known plastic recycling waste streams. For instance in Figure 2 we can see how pure, binary, ternary, and quaternary plastic waste mixtures behave under pyrolysis conditions with different catalysts.
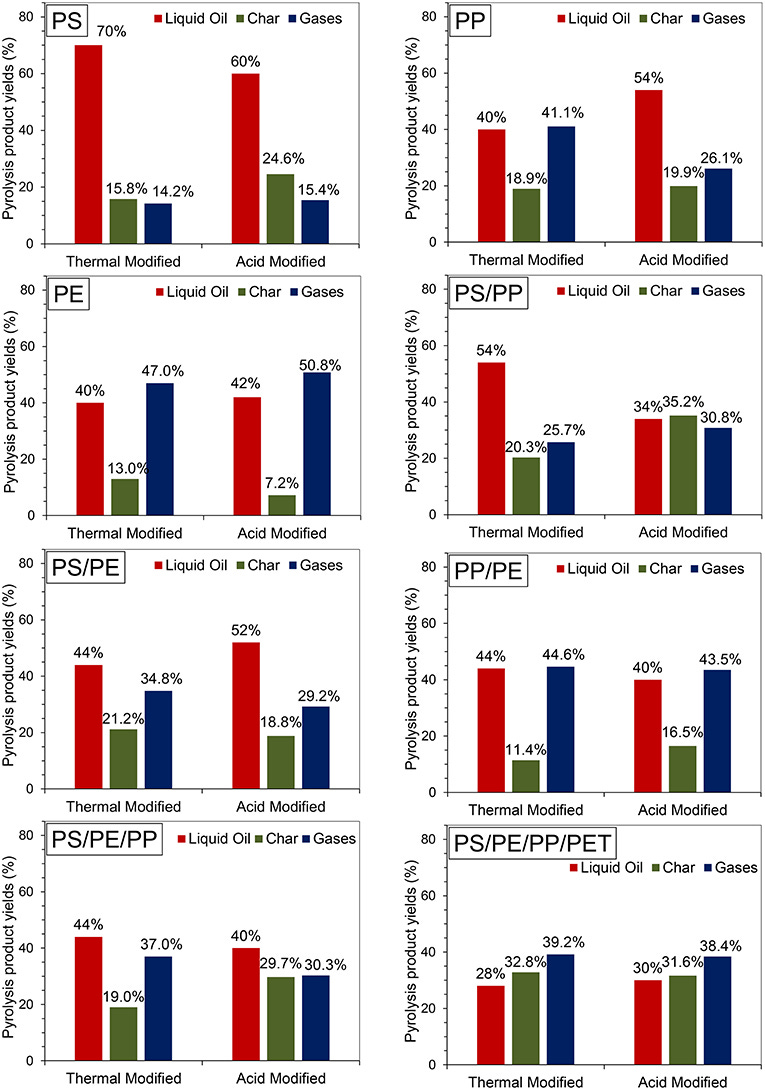
One thing that should hopefully jump out to you is that the polystyrene pyrolysis products predominately are oils both with the thermal and acid modified catalyst. Investors and the chemical industry have also taken note that pyrolysis of polystyrene can produce a high yield of liquid and may provide a new outlet for all of the consumer polystyrene foam that is difficult to recycle.
Is Anyone Doing Plastic Pyrolysis?
C&EN reported in late 2019 that one of many companies working on pyrolysis of plastic waste called Agilyx (I hope the wordplay on agility is not lost here) had successfully built a pilot plant capable of processing 10 tons/day of polystyrene via pyrolysis. Successful demonstration of chemical recycling at scale is the thing that most chemical companies need to see before they are willing to enter partnerships with start-ups or even begin doing the necessary R&D work to look at new products or license a new technology. Additionally, because Agilyx holds IP on their process and are investing into R&D, the ability to license their technology out to larger integrated companies like Sabic is another revenue stream on top of selling products from their growing chemical recycling business. Figure 3 shows the closed loop marketplace envisioned by Agilyx and the role their customers might play in the plastics supply chain.
One benefit that chemical recycling has over melt reprocessing of existing plastics is that it is a route to overcome the regulatory restrictions on food contact materials. The barrier properties for instance on recycled PET (rPET) will not be as robust as virgin PET. Chemical recycling enables consumer packaged goods companies to make their packaging circular while also not having to worry about any sorts of regulatory approval issues from government agencies. An example of this type of recycling happening I talked about in a Friday newsletter where a consortium of chemical and plastics companies are making multilayered packaging for meat food contact applications from mixed-use chemically recycled feedstocks.
Chemical Recycling Can Expand Recycling Of More Materials
A large portion of food packaging materials are multilayer laminates where each layer of different plastic serves a very specific purpose. The problem with laminates is that they cannot be physically recycled and are not accepted in traditional recycling streams now. Chemical recycling could in theory expand what we consider to be recyclable plastics and have the agility to create a diverse amount of end products from the oils and gases produced based on market demand. Mixed plastic waste could be the 21st century version of crude oil.
The Chemical Industry and Wants This To Happen
The American Chemistry Council is the main trade advocacy group for the chemical industry (lobbyists) and they have formed a special division called the Advanced Recycling Alliance for Plastics with the sole mission to educate the public and policy makers about how chemical recycling of plastic works and why it might be beneficial.
I expect installation of chemical recycling capacity will grow over the next decade and that single source streams of polystyrene, polyethylene, polypropylene, and polyethylene terephthalate will command premium value while well defined mixed-use plastic streams will be of lesser value.
Less Dependent On Oil Prices
Low oil prices make traditional recycling of plastic (melt reprocessing) really uneconomical. C&EN’s Alexander H. Tullo spoke to Nina Bellucci Butler of More Recycling about the challenges of low oil prices and utilizing traditional recycling methods on plastic waste.
In the early 2010s, Butler says, companies were investing in, and plastic goods makers were increasingly using, recycled material. That faded when oil prices tumbled. Recycling isn’t attractive when oil is below $100 per barrel, she says. “Companies aren’t ready to pay 20% premiums for a product that is not at the same level of quality as virgin unless there is a marketplace incentive to producing a product with a lower carbon footprint.”
I think chemical recycling could be a way around the low oil priced future I’ve spoken about and I believe oil companies themselves want to diversify their income streams away from traditional refinement and extraction of oil post Covid-19. I believe that chemical recycling of plastic and processing the products for an oil company will be a strategic move that many companies will make in the next few years. Shell announced about a year ago they planned on using a million tons of plastic waste in their plants by 2025—before Covid-19 sent oil prices plummeting and we had negatively priced oil futures.
I suspect a small amount of public policy from governments around the world could help speed up this transition to this new recycling method and help lower the barrier of entry for building secondary sorting facilities. I will think about what types of public policy initiatives might be useful in the coming weeks.
Conclusion
Solving the plastic waste problem means thinking about used plastics as a new raw material that has a defined value by the market and chemical recycling is a key factor in making this happen.
For those that want to dive into the details on some of the information I’ve provided here are my references: A review article here, an article on catalytic pyrolysis of single and mixed plastics here, C&EN article here and the investor presentation from Agilyx here.
Next Steps
In the next few weeks I will look to bring this series to a close, condense it all, and publish it into something more accessible to a broader audience. My next planned topics are traditional recycling of plastics, biobased and/or renewable polymers, biodegradable plastics, and how public policy might also play a role.
You can only solve a problem when you understand it
Tony
The views here are my own, do not represent those of my employer, should not be considered investment advice, and before using any chemical you should read and understand the safety data sheet.