Monday morning was trash and recycling day for my neighborhood. Our recycling bin was full, our compost bin had quite a bit of food scraps, and we kept our trash in the house because it was only half full after a week. Last month for a few weeks the town of Arlington, Massachusetts has sent an employee around early Monday mornings to check our recycling and make sure certain plastics did not make their way into the recycling stream. Plastics like films from food packaging, low density polyethylene, polystyrene foam, and Amazon bags got your bin tagged and your recycling did not get picked up until you fixed the problem. The purpose of doing this was to help make the recycling stream cleaner and more readily to sell to a processer for mechanical recycling. As a resident wondering what types of recycling are allowed Arlington sends you to an NPR story that essentially makes it more ambiguous, but essentially only HDPE, PP, and PET are the preferred plastics for recycling.
Chemical recycling covered in Part 3 could enable expanding our recycling stream if the technology became capable of handling a variety of mixed plastics. The plastics we can recycle now are primarily comprised of what is in the Big Six as covered in part 1 and part 2, but not everything. Plastic recyclers find of value in our curbside recycling through PET, HDPE, and to a lesser extent PP.
Recycling Route 2: Mechanical Recycling
Low Demand = Low Pricing = Too Expensive to Recycle = Landfill
I believe that chemical recycling is the future and it is a key in saving us from drowning in plastic waste, but mechanical recycling is what we have known for decades and it is a valuable and viable method for recycling plastic, specifically HDPE, PP, and PET because there are uses for them.
If we look at the numbers from the EPA we can see that recycling volume is small compared to landfilling and the problem is primarily one of economics—not capability. Recycling plastics through melting is not as easy as it might sound.
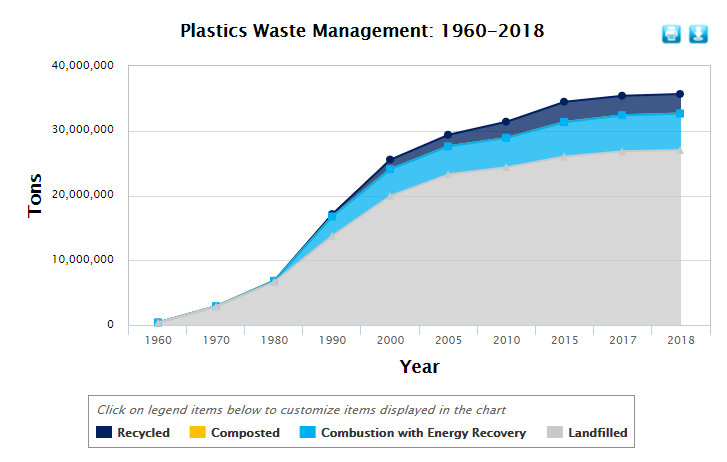
I plotted the EPA’s data into Figure 2 to look at how recycling has gained adoption since the 1990s, but overall it seems to have peaked at about 9% in 2015 and then dropped to about 8-8.5% in 2017 and 2018.
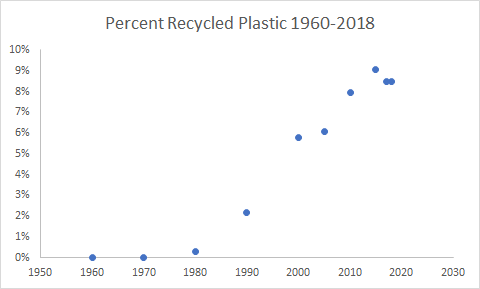
So why does so much go plastic go to landfills and not into other stuff? This is a really complex question that I’m not sure I can answer here. My back of the envelope calculations in Figure 3 take into account what I could find on actual pricing of recycled HDPE, PP, and PET in 2020 versus the average cost to recycle plastics in the US over the last 5 years. Some of the data is a bit mismatched based on time and the price of recycled plastics fluctuates dramatically.
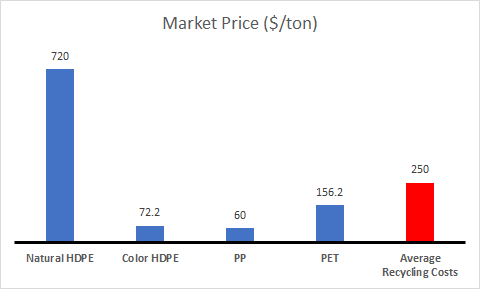
Essentially right now in the United States it appears to cost more to recycle color HDPE, PP, and PET whereas natural HDPE (no color) commands the highest price and seems to be economically viable. This is why shipping our plastic waste to China was beneficial, lower costs on recycling, and more advanced equipment. The figure from the start of the series might be more helpful now. I would not be surprised to learn that we are landfilling more plastic in 2020 than we have previously.
Another source that is helpful is McKinsey’s analysis of plastic recycling. They have an excellent report here with two figures that are useful to fully understand the challenges of traditional recycling. The figures come from McKinsey’s economic model.
From Figure 4 we can see that PET at the time of running the model was quite valuable in North America whereas polypropylene in Europe would yield little profit. Plastic waste from electronics and other material in Figure 4 actually represent a negative EBITDA, which means you would lose a lot of money if you tried to recycle those materials. That loss on recycling could be partially driven through trying to recycle thermosets in electronics or low density plastics like polystyrene foam.
McKinsey’s second figure worth discussing looks at return on invested capital.
My takeaway here is that to actually install more capacity to recycle more plastics only about 20% of all the plastics made right now would actually provide a return on investment. In the United States we are already nearing about half that capacity with our 8.5-9% recycling rate.
Essentially without some sort of massive government subsidy recycling plastics is not very economically viable. Economic viability of recycling is what puts a recycler in business.
The video below has a good example of what it takes to actually recycle PET from sorting to washing to cutting to disposing of the waste water.
How Does This Type of Recycling Actually Work?
Now that we have the economics somewhat covered how does this process actually work once we have the raw material ready to go?
The first step would be to have the chips of plastic fed into an extruder and then transformed into into either pellets (to be processed into its final form) or directly transformed into the final form such as the actual plastic part, which could be anything from films to bottles to fibers to cups. A good visual explanation of the extrusion and molding process can be found in the video below and covers many of the actual forming aspects of plastics production.
There are some finer details such as sometimes needing to dry the resins prior to extrusion and incorporating additives such as light stabilizers and antioxidants or some sort of master batched additive to impart color or unique properties to the end product. The final product may also be laminated with other plastics to provide gas barrier properties (think food packaging) or blended with other plastics to provide a unique set of physical properties such as impact strength.
One of the benefits of mechanical recycling work is that we do not need to do any chemistry to the plastics before they can be used again, but the end uses may primarily be relegated to non-food contact applications such as textiles and apparel. However, if regulations change food contact recycled plastics may become a reality in the near future and the current requirements for recycled plastic for food contact applications by the FDA can be found here.
We should consider mechanical and chemical recycling to be complimentary to each other and both are tools that we will need to use to solve the plastic waste problem. I’ll write about recycling method 3 next week.
Tony
The views here are my own and do not represent those of my employer nor should they be considered investment advice.